Chad Twombly, business manager at Herculite Products Inc., York, Pa., wrote a blog on this topic recently. I followed up with a phone conversation with him. The result, I think, provides some clarity and useful information, particularly for end product manufacturers who may not be accustomed to working with these products.
~ Janet Preus, senior editor
When Twombly gets a call from a customer that needs an antistatic material, his first question is, “What level of static dissipation do you need?” Often, there’s silence on the other end of the line. “Too many people don’t understand what they need,” says Twombly. “The majority of the people don’t understand the difference between surface electrical charges and electrical current. What we’re trying to address with our products is surface electricity,” he says.
What they need is an ohms test to find out. “Ohms testing is really important,” he says. “It gives them a quantifiable way to pick the right solution. That will help them to determine what level of protection they need. Somebody knows, and they need to go back to that person and find out.”
For instance, a very conductive fabric is required if microchips are involved. If the microchips are components in explosives, such as a weapons system, there is no room for error. A much lower level of dissipation is needed in basic health care situations; for example, there is a need to control static electricity in fabrics when a patient is transferred to a gurney.
Both of these market areas—health care and industries that use microchip technologies—continue to be strong. There are other industrial settings where static dissipative textiles are essential. Lots of products loaded into containers can generate static electricity. “Any place where there is surface or static electricity, they need to be cautious,” he says. Recently, Twombly was asked to provide an antistatic fabric for a client that was transferring resin into rail cars, the customer was trying to dissipate the static electricity that was gathering from the movement of the resin through the chute; the collection of static energy was causing the resin to “stick” to the chute.
Electricity 101
If your level of expertise in the area of electricity and static electric charge doesn’t extend as far as high school physics, basic information that Twombly outlined in his blog post is a good starting point. To understand the difference between antistatic, dissipative and conductive, as it relates to electricity and fabrics, it is helpful to first understand the difference between the terms insulation and conductive as it relates to electricity.
Conducting energy is able to transmit energy, particularly heat or electricity. Conductors are materials that permit the flow of electric charges in one or more directions. Metals are particularly conductive, which is why they’re used to move electricity in the form of electric wiring, for example.
Electric insulators prevent or reduce the passage of heat, electricity or sound—just the opposite of electric conductors. In these materials, internal electric charges do not flow freely, and so they limit the flow of electricity. The PVC and paper used to wrap the electrical wire are examples. The insulators on an extension cord obviously prevent the charge from passing through them so you don’t get shocked.
As a rule, PVC makes a good insulator, but there are things that can be done to make PVC engineered textiles more conductive. The level of manipulation to the material to change its conductive properties will put it into one of three classifications: antistatic, static dissipative or conductive.
Here’s how the MIL-HDBK-773A DOD [U.S. Military] Handbook classifies these three:
- Antistatic refers to the property of a material that inhibits triboelectric (static electricity) charge generation effects
- Static Dissipative materials rapidly dissipate electrostatic charges over their surface or volume, having a resistivity range between conductive and insulative
- Conductive materials are either surface or volume conductive and may be either metal or impregnated with metal, carbon particles or other conductive ingredients, or may have a surface that has been treated with such materials through a process of lacquering, plating, metallizing or printing.
To determine if materials meet one of these three classifications, testing is done for surface resistivity that is measured in ohms/square.
When designing a product solution it is important to understand the demands of the specific application. When dealing with the engineers or designers, it is recommended that you ask for the ohms level required to make sure the materials chosen are the right ones.
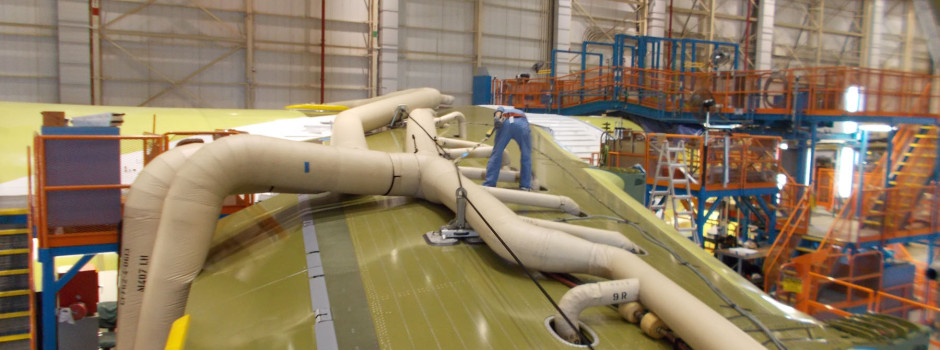