New materials and compositions for fabrics spur innovative products.
by Marie O’Mahony
Health and safety are proving to be key drivers for innovative new fabric structures. These can prompt new designs in existing products and devices, or even whole new products. This is possible with imagination, expertise and an openness to look for solutions outside conventional thinking.
Strength can, of course, include hardness, but to be truly effective it may also need to be flexible rather than rigid, particularly when worn on the human body. An understanding of the importance of comfort to performance and user acceptance has prompted a welcome evaluation of materials, particularly where there is weight saving to be made or a design innovation. Three developments from different global regions illustrate the potential for novel textiles to guide design and deliver medical and protective benefits to the user.
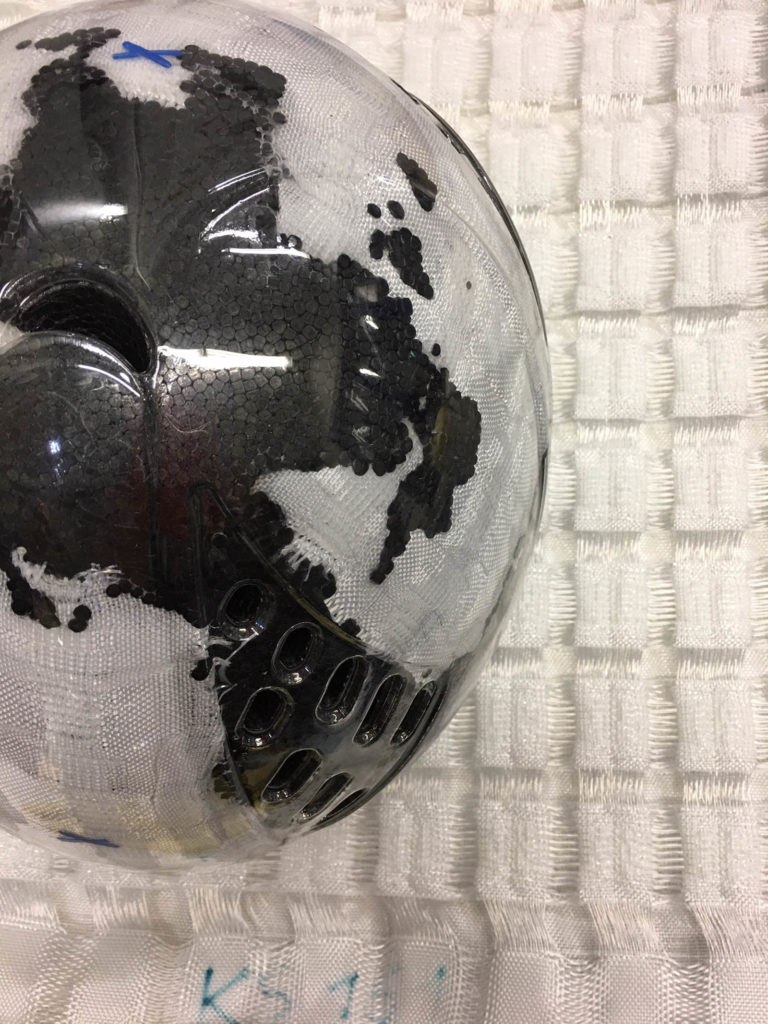
A layered approach
A 3D weave coupled with foam has been shown to provide an ideal structure for impact absorption and dissipation in protective helmets. Researchers at the Deutsche Institute für Textil und Faserforschung Denkendorf (DITF) are utilising a 3D weaving process to produce a spacer fabric that can be foam-filled and molded to form the basis for a three-dimensional spherical structure such as a ski helmet.
Fiber use and placement can be optimized so that additional fibers can be used in the outermost layer where full coverage is required, but innermost towards the head a grid-like formation provides for a snug fit with minimal contact points. This approach maximizes the capacity for shock absorbency while at the same time reducing weight and material use. The combination of woven spacer and particle foam is shown in testing to increase the capacity for shock absorption by 30 percent over conventional designs.
Tatoo-inspired
Patients undergoing surgical treatment for throat cancer can suffer from a temporary or even permanent loss of voice, as well as risking facial disfigurement. Researchers at Soochow University in China and the National University of Singapore are developing a very thin tattoo-like epidermal patch as a Human Machine Interface (HMI) to improve a patient’s ability to communicate. The patch is able to record surface electromyography (sEMG) created by the patient’s facial muscles and jaw movement that allows for smart voice recognition, voice synthesis and virtual interaction.
Until now measurements have relied on the use of rigid electrodes attached to the skin using gel and adhesive tape or straps that are not well suited to daily use. The new device can be more discretely attached to the face or jaw, and uses advances in soft, flexible electronics with a sterile wound dressing sandwiched between the face and patch, providing protection and adhesion.
Tremor control
Researchers in Switzerland led by Empa, Swiss Federal Laboratories for Materials Science and Technology are developing an adjustable, inflatable textile orthotic for wrist tremor suppression in patients. Essential Tremor (ET) affects an estimated 2.2 percent of the U.S. population over 65 years, with Parkinson’s Disease (PD) the second highest group suffering from movement disorders. Neither are curable, with tremor suppression orthoses one option.
The researchers used a textile “glove,” designed to be easy to put on and take off, low weight, flexible and non-irritating to the skin. Air inflating the membrane structure allows for variable stiffness that can be regulated by the user. This can be adjusted for specific tasks either with a hand pump or a small switch-activated electrical pump.
An innovative new laser-welding technique uses an infrared laser to create a mechanically strong but flexible seam. The flexibility it allows for—in a range of 3D shape designs—is greater than what is possible with more conventional methods, such as hot press. The resulting orthosis offers a lightweight design, weighing just 33g, helping to prevent muscle fatigue.
This is particularly important when used over long periods of time, or for elderly patients where there is a high risk of skeletal muscle mass. Tests that have been undertaken with three of six key tasks (drinking from a cup, pouring water and drawing a spiral) are showing positive results.
While it may be simplistic to say that in looking at the potential for advanced and smart textiles in health and safety we should just look at replacing heavier or less flexible materials with textiles, there is still much to be gained by looking afresh within the textile sector itself. In these few examples we see how weaving can be sandwiched with foam in new ways, how flexible electronics and wound dressings can benefit one another without full integration, and how a new laser welding technique can open up opportunities for textile structures. Solutions are in the detail and in the creative vision.
Marie O’Mahony is an industry consultant, author and academic. She is the author of several books on advanced and smart textiles published by Thames and Hudson and Visiting Professor at the Royal College of Art (RCA), London.