The Innovation Award is presented annually by the Industrial Fabrics Foundation (IFF) to one exemplary company for an entry that is distinctive from other products currently manufactured or processes in use; benefits the specialty fabrics industry or consumer; is practical; and is cost-effective. The purpose behind the Innovation Award is to inspire companies from all over the world to not only come up with great ideas, but to also make them happen. Four companies were recognized for excellence in their categories.
Innovation Award winner
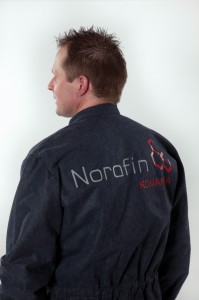
Norafin Komanda nonwovens for arc-flash protection and flame-resistant protective clothing took home top honors in this year’s competition. Entered in the Fabrics, Fibers and Films category, the Komanda brand represents a range of performance-engineered nonwoven materials that deliver significant advantages over traditional textile materials used in arc-flash protection and flame-resistant protection.
Innovations include arc thermal-protective performance (ATPV) that is nearly triple that of competitive materials at the same weight, or the same level of ATPV performance at up to 45 percent lower weights. As a stand-alone material or in layered or laminated constructions, Komanda elevates the level of protection and comfort that can be offered to the arc-flash protective clothing market.
Highly breathable, Komanda maintains its high performance after 100 industrial laundry cycles. Its inherently flame-resistant fibers provide protection for the life of the garment. Arc performance, weight, durability and other performance qualities can be customized to meet individual customer requirements. It is currently used as a liner material in a jacket.
The fabric is going through final stage evaluation in the European and U.S. markets for sales in all global markets. Norafin Americas Inc. is headquartered in Ashville, N.C.
Honorable Mention
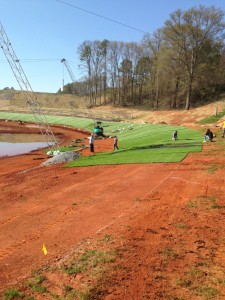
Hydro Turf™ Advanced Revetment Technology, submitted by Watershed Geosynthetics, Chattanooga, Tenn., received honorable mention in the End Product category. A unique, fiber-reinforced concrete armoring technology, Hydro Turf is used to prevent erosion under severe hydraulic conditions.
It consists of a high-friction, structured geomembrane with an integrated drainage layer overlain by an engineered synthetic turf, which is infilled with high-strength concrete. The product provides benefits over traditional revetment solutions (i.e., rock riprap, concrete paving, articulated concrete block), including superior hydraulic performance; lower construction and maintenance costs; rapid, low impact and scalable installation; reduction in carbon footprint; and the aesthetics of natural turf.
Economical and eco-friendly, it offers erosion protection in applications that include levee overtopping, dam spillways, flood control and drainage channels, basins, shorelines and slopes. HydroTurf performance has been well documented through testing in laboratories and project applications.
By resisting severe, five-foot continuous overtopping flows, simulated 500 year (Category 5) hurricanes and 120 mph winds, it has established a new standard for the erosion-control industry. Currently, there are approximately 10 project installations in United States and Europe; 20 projects that will bid to install this year in the U.S. and Canada, and another 60 projects that are under consideration and design in North America, South America, Europe and the Middle East.
The U.S. Congress recently passed the Water Resources Reform and Development Act, a $12.3 billion bill that provides funding for levees and dams, both of which require revetment armoring, so it is conceivable that in three to five years HydroTurf will have a 5 percent market share and a 20 percent market share or better in the longer-term future.
Honorable Mention
Vacu-Wash®, Greenland, N.H., offered a product of the same name in the competition, earning honorable mention in the Hardware, Findings and Accessories category.
Vacu-Wash, an eco-friendly cleaning system, was used to clean this sail, shown in a “before and after” photo. Vacu-Wash USA is located in Greenland, N.H. Photo: Vacu-Wash.
Vacu-Wash® is a new and innovative method of removing mildew and other contaminants from films and fabrics in a gentle and environmentally safe way. The basic process involves placing the item in a specifically designed vacuum chamber where a cleaning agent is introduced. Without any air pockets remaining, which would prevent the cleaning agent from coming into contact with the surface of the film or fabric, the film or fabric is thoroughly cleaned without any agitation or abrasive action. This process is especially effective on lighter materials, such as those used in outdoor acrylics, sailcloth tents and other laminated materials.
This technology could have quite an impact on the wedding tent rental industry, which needs a reliable and safe way to provide pristine clean tents for functions. Outdoor patio furniture cushions, umbrellas and fabric products in marine applications are also prone to mildew, so these market areas could also benefit from this process.
Glen Raven Inc. recently approved Vacu-Wash for cleaning their U.S.-made Sunbrella® fabrics. The process is available in Australia and Europe, as well.
Honorable Mention
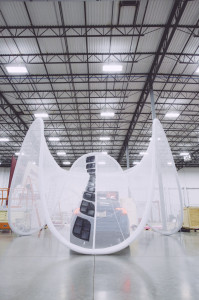
The PURE Tension Volvo Pavilion was a collaborative effort between Synthesis Design + Architecture (SDA), Buro Happold (BH) and Fabric Images Inc., Elgin, Ill. The design began as a concept commissioned by Volvo Car Italia to showcase the new Volvo V60 plug-in hybrid vehicle. The purpose was to create a lightweight, rapidly deployable, tensioned-membrane structure that would act as a portable charging station—and fit inside the trunk of the car.
The goal was to fabricate a reliable, functional solution for addressing the issue of sustainability and provide recharging for the Volvo line of hybrid vehicles. One of the benefits was the power strategy incorporated into the architecture which enabled the photovoltaic panels to collect enough energy to power and charge the Volvo V60.
What started as an experimental concept was brought to life through dedication to the design and an understanding of the vision and purpose of the project. What set it apart was how the application actually functioned; many people—even at Volvo—weren’t sure this could be built.
A distinct benefit was its lightweight, deployable functionality, with the relatively simple perimeter aluminum framework tensioned in place with the help of the fabric cover: the frame pushes out while the skin pulls in, creating a lightweight, cost-effective and easily transportable solution.
Because patterning of the fabric could not be figured through typical tensile patterning methods, a digital form was exploded into non-uniform quadrilaterals to allow for the digital mesh to become successfully unrolled into hundreds of tiles that were CNC cut-and-sewn to fit like a glove. A total of 518 tiles of fabric were quilted together, combining tension and shape.