Fiber-based composite development sparks special interest.
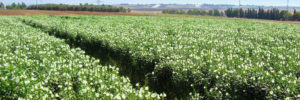
Composites is a high-growth industry and, according to two major market intelligence groups, will reach more than $100 billion by 2022. Paris-based JEC Composites has estimated that this sector grew from $75 billion to $82 billion in one year during 2015-16 and will reach a value of $103 billion by 2021. MarketsandMarket™ estimates that the CAGR of this sector will be about 8 percent, and the market value will reach $115 billion by 2022.
An interesting fact is that this sector’s growth will be above the GDP growth rate of developed economies such as the U.S. and Europe. This positive growth figure provides confidence in the sector, which is vital for continuing investments.
A new understanding of composites
Composites are hybrid structures that are formed using multi-components to achieve desired properties for specific applications. The hybrid structure arises due to the use of varying materials, such as different fibers or using different structural forms made out of the same material. For example, soft composites can be made out of cotton in woven and nonwoven forms to obtain greater sound absorption (attributable to a nonwoven structure), improved strength and structural integrity (attributable to a woven structure).
Composites can be broadly classified into flexible (soft) composites and rigid (hard) composites. Hard composites involving plastics and metal matrices are common and have found many industrial applications such as in automobiles, aerospace and other heavy engineering applications. Soft composites, although pliable structures, are strong in order to accomplish the desired performance and are used in both industrial and consumer applications.
In addition to these two categorized classifications, there are composites involving both soft and hard components termed hybrid composites. These are better as flexible rather than rigid structures; fiber-based composites would be an example. Fibrous materials are viscoelastic in nature providing resiliency, an attribute that’s beneficial in developing composites that have human interaction, such as for body armor.
Interest in fiber-based soft composites
Fibrous composites, such as fiber-reinforced plastics (FRPs), have penetrated into industrial applications. The textile industry has been adopting blends—which are, in a way, some form of composites—to achieve a balance of desired characteristics and cost. In the present times, a good example for a fiber-based soft composite is a nonwoven wipe.This product is a classic model for obtaining a balance of cost and characteristics while penetrating into the consumer market place. It represents a diversion for soft composite structures to focus on single-use consumer products, such as personnel wipes.
As these pliable, soft composites target single-use and semi-durable market space, consumption increases and hence their market value goes up, too. A recent report by Smithers PIRA estimates the current nonwoven wipes market to be $16.6 billion and is estimated to reach a value of $21.8 billion by 2023.
Soft, blended wipes are generally classified as personal care, home care or industrial wipes. Personal care wipes include baby wipes, which are predominantly blends of the same wipe structure, while others involve hybrid structures. Natural fiber including blended single- and multi-layer wipes are the emerging development in the soft composites sector.
The growing awareness about environmental pollution, even in densely populated growing economies like India, is creating a shift from using synthetic and plastic-based materials to natural fiber-based materials. The Indian government, as part of 2018 World Environment Day activities, has announced its plan to avoid using single-use plastics by 2022. For instance, highly industrialized states in India such as Tamilnadu and Maharashtra are implementing policies to avoid plastic pollution, which puts necessary pressure on textiles and other industries to develop biodegradable products. These recent major initiatives in India and other parts of the world provide ample opportunities for the composites sector to invest in environmentally friendlier R&D.
The U.S. and Indian governments have invested heavily in composites research already. Through the National Manufacturing Network Initiative, an advanced level composites research institute has been established at the University of Tennessee, Knoxville. Likewise, the Indian government in its plan to grow the technical textiles field, which encompasses composites, has invested in two Centers for Excellence to focus on research-related to composites and allied materials: the Research Institute in Coimbatore that will focus on industrial textiles; and the Research Institute in Ichalkaranji that will focus on nonwovens.
New developments
An interesting development that started more than a decade ago is a transatlantic partnership between the University of Bremen, Germany; the U.S. Department of Agriculture (USDA); the Agricultural Research Service (ARS), New Orleans; and the University of Tennessee. This partnership looked at the use of cotton to develop natural fiber-based composites for automobile parts. The overarching goal was to reduce the use of plastic-based parts in an automobile and develop quality door panels, headliner components and other parts out of natural materials. Success resulted in the development of acoustic insulative, high-loft materials.
Research into the use of alternate natural fibers such as kenaf for industrial textiles, was pioneered by Prof. Gita Ramaswamy of Kansas State University. Similar research was also carried out at the University of Arkansas, which looked at the use of kenaf and cotton blends to develop soft composites. A USDA funded project at Auburn University looked at the use of chicken feathers in developing composites for a myriad of applications.
Military, pollution control
Hybrid composites involving soft and hard materials find an important place in the defense and aerospace sectors. Wovens, knits and nonwoven structures are used in the development of such composites. In many applications, the porous structure of nonwovens comes in handy, where insulation and absorption characteristics are required. Additionally, staple fiber-based nonwoven manufacturing processes, such as carded thermalbonding, needlepunching and hydroentangling, can be used as interconnecting processes to develop flexible composites.
The carded nonwoven process has been effectively used to develop soft composites that find applications both in defense and pollution control. One product utilized the needlepunching process to develop an adsorptive-absorptive, layered, flexible composite to quickly wick away volatile organic compounds, such as sulfur mustard and pesticides. These pliable wipes are used to clean intricate parts of fighter planes, military equipment and human skin, in the event of a toxic spill.
The technology used the highly productive and cost effective nonwoven process (compared to weaving). This model of cost and technology balance has resulted in speedy commercialization. Chantilly, Va.-based First Line Tech has taken the product to market and the product is currently used by government agencies.
While these soft composite use different fibers to develop a layered material, the same process has been manipulated to develop hybrid structure involving woven and nonwoven forms. Tex Tech Industries, with headquarters in Portland, Maine, has used needlepunching technology to develop soft, body armor panels. Nonwoven layers interconnect antiballistic woven layers providing enhanced protection. Recently, Chennai, India-based WellGro Tech has used the hybrid concept to develop highly biodegradable composites that can separate oil from water to help with marine pollution and oil spill cleanup.
Fiber-based soft composites also have applications in the biomedical and filtration sectors. A few decades ago, St. Paul, Minn.-based Donaldson Company pioneered the use of nanofiber composites to develop high-efficiency filters. Nanofibers due to higher surface area could adsorb fine particles, while minimally affecting the pressure drop. These days, nanofiber production technologies have improved where standalone nanofiber webs can be developed with improved strength and durability.
Researchers at the University of Connecticut have developed environmentally friendly silk composites, which can be used to support broken bones. A team led by Prof. Mei Wei has used silk fibroin to develop these composites, which are strong and at the same time flexible. Besides silk fibroin, polylactic acid is used and it’s coated with hydroxyapatite.
The way forward
Some of the challenges facing the industry are prompting composites to be made more cost effective, with reduced weight and having equal or improved performance against metal matrices. Important characteristics such as toughness and flexibility have to be accomplished in soft composites for use in both industrial and consumer goods. While nonsynthetic-based natural-fiber composites are attractive alternatives, there needs to be a balance between cost and efficiency for success in the marketplace.
Seshadri Ramkumar, Ph.D., is the director of the Nonwovens and Advanced Materials Laboratory, Texas Tech University, and a frequent contributor to Advanced Textiles Source.