New developments address power and its integration into the production process—for whatever applications can be imagined.
by Marie O’Mahony
The means chosen in energy provision for smart textiles is largely dictated by the application, or, more precisely, the needs and behavior of the user. This is a meaningful development, taking it from the typical questions (energy level needed, weight, size and environmental impact), to a more nuanced approach. The new solutions in development will certainly impact tomorrow’s products, from wearable technology to automotive applications.
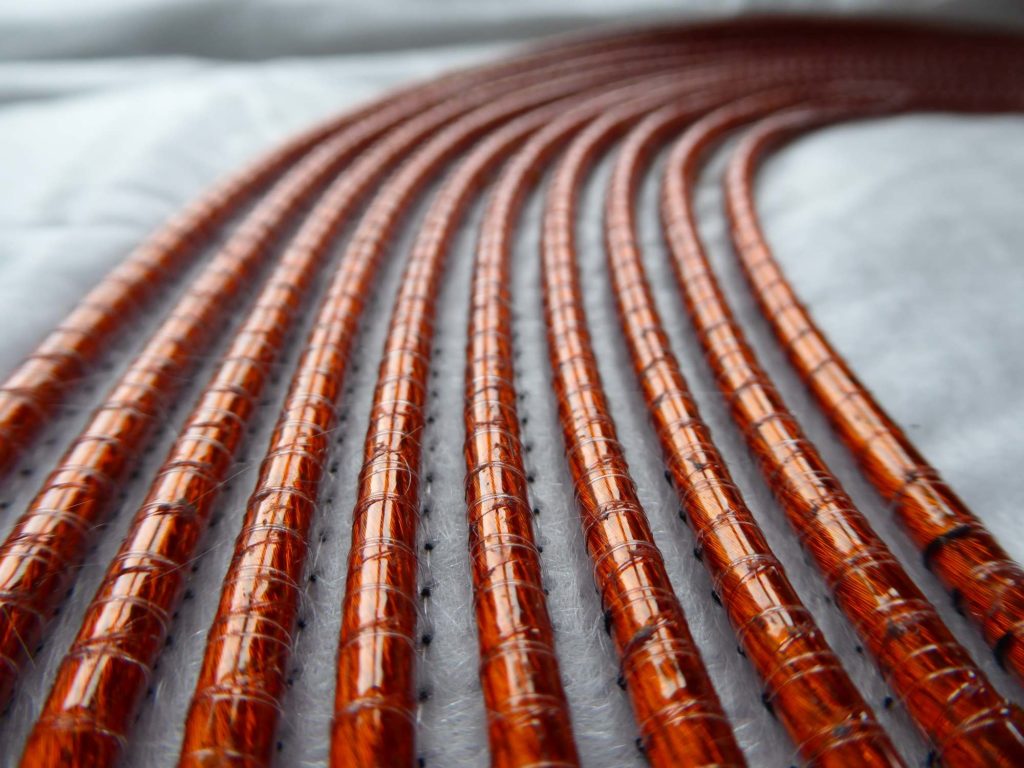
Flexible, lightweight, powerful
New developments in energy for smart materials and systems for wearable technology are addressing power and its integration into the production process. For the consumer, the result is a more compact, comfortable and seamlessly integrated product.
Professor Zijian Zheng and his team at the Hong Kong Polytechnic Institute of Clothing have developed a compact, lightweight, flexible, high-energy textile lithium battery. The thin, metal film used in conventional lithium batteries has been replaced by a metallic coated fabric. This is further coated with cathode and anode materials turning it into an electrode.
In the final stage, the material is assembled into a pouch making it compatible with roll-to-roll manufacturing of textiles and conventional battery production lines. This is part of a growing trend in research to take greater account of the full manufacturing process even when concentrating on a single part of the process.
In its report, “Flexible, Printed and Thin Film Batteries 2019-2029,” IDTechEx expects the primary demand in the future to be for large-scale product (IoT and electric vehicles, for example), which would generate a need for new battery designs that traditional batteries cannot fulfil. This is paving the way for innovation in battery design and providing opportunity across all industry sectors including smart textiles and wearable technologies.
Canada’s Pliant Power produces customizable, high-energy, rechargeable, printed, flexible Lithium batteries for applications such as wearable technology. Using a silk-screen printing process, size and shape can be tailored to the customer’s needs and are sold direct to the customer. From an environmental standpoint, its batteries are a distinct improvement, as no heavy metals are used, and the inks are water-based.
Carbon fiber for electric vehicles
Electric vehicles are still at a relatively early stage of development and consumer use, but the enthusiasm and market is there. Itself a disruptive technology, it’s causing technologists to give serious consideration to energy: its source, supply and charging speed.
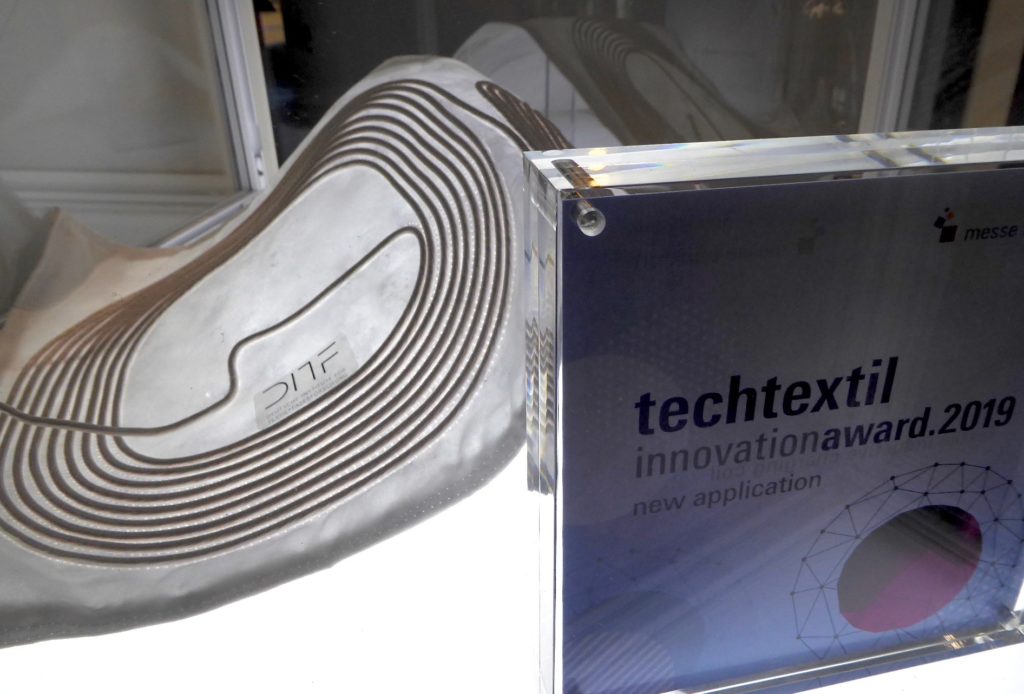
The electric vehicle highlights the fact that the car of the future must come from multiple stakeholders working together ensuring that the transport system is prepared. I still remember the delight of the French Eurostar drivers as they informed passengers of the difference in speed as the train passed from English train tracks to the superior French ones. Two examples illustrate improvements to the product (car) and innovation that applies to a more holistic approach that involves both the vehicle and the road that it travels on.
Researchers at ITA RWTH Aachen are utilising a new filament winding technology to make a Composite Pressure Vessel (CPV) for the emission-free remote-controlled RC-Car. Manufactured using carbon fiber there clearly saves weight, compared to a conventional battery source. That increases with the use of multifilament winding where the mandrel rotates and moves back and forth horizontally while the reinforcing carbon fibers are positioned. During the rotation a complete layer is placed down on the mandrel, at once reducing manufacturing times and increasing preform productivity. The CPV is used to store hydrogen that is seen as an environmentally friendly power source.
In April 2019 California had just thirty-nine hydrogen refuelling stations but industry-watchers envisage demand and technology pushing this number to reach as many as 1,000 stations by 2030.
Recharging buses en route
The German Institutes of Textile and Fiber Research Denkendorf (DITF), Beira Interior University (DCTT), Portugal, and Robert Bosch GmbH are developing a textile inductive charging coil designed to allow busses to recharge while en route. DITF’s Sathis Kumar Selvarayan envisages the system being used on urban streets.
As the bus stops to let passengers on and off the average time of two minutes is enough to allow the recharging to take place. The charging station is embedded in the road surface by the bus stop and the charging coil positioned in the undercarriage of the vehicle that comes to a stop just over the charger.
The project is conducted under the ARENA2036-LiFu project, with its goal to be “the lightweight design with integrated functionality in the versatile factory of the future …. a pacemaker for sustainable automotive engineering for the next generation of cars.”
The European Union-funded research program is focused on long-term planning, all the way to 2036. While there is growing interest in contactless charging using conductive coils for electric and plug-in hybrid vehicles, their size is an issue. Embroidery technology is useful in this development, because it can allow for very precise positioning and control of the copper strands and polyester embroidery threads avoiding damage to the metal during placement.
Once the embroidery process has been completed, a further composite consolidation process is performed. This results in the building of a glass fiber-reinforced plastic, protective casing and integrated ferrite isolation material and heat dissipater. Textile-based deformation and impact sensors are also integrated into the composite in a process that the researchers expect to be scalable and capable of being highly automated.
Perhaps the most significant contribution that these innovations afford is not in their individual application sectors, but in what they offer the supply chain landscape. Providing energy is just a starting point. That all of them are taking account of where they fit in the production process is important. That electronics and textile are drawing closer together as a hybrid is indicative of the new partnerships that may emerge.
Marie O’Mahony is an industry consultant, author and academic. She the author of several books on advanced and smart textiles published by Thames and Hudson and Visiting Professor at the Royal College of Art (RCA), London. www.linkedin.com/in/marie-o-mahony-94776836
Professor Zheng Zijian of The Hong Kong Polytechnic’s Institute of Clothing describes the benefit of their newly developed flexible Textile Lithium Battery.