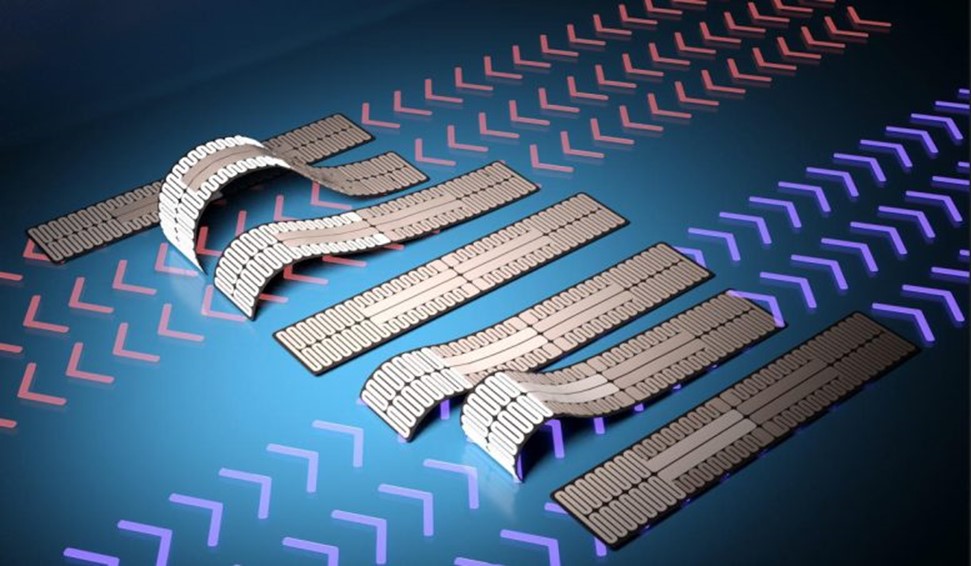
The advanced textiles industry is comprised of a majority of small and medium enterprises (SME), which also form a growth sector for the industry. But its development and growth depend on being nimble and creative. In the post COVID-19 era, major economies, such as the U.S., U.K. and India, are supporting the rejuvenation and growth of manufacturing. The area that is getting added attention is sustainability in general, and carbon footprint reduction, in particular.
Growth in different subsectors of the advanced textiles industry is expected—if the focus is on sustainable, value-added products, green manufacturing, circularity, energy and cost savings, and resource conservation. An optimistic picture is expected if these sectors cater to national defense, human health, lifestyle improvement and environmental protection markets.
Sectors such as aerospace, automotive, personnel protection, medical, and infrastructure will provide opportunities for the advanced textiles industry to diversify and grow. Processing methods and supportive technologies, including smart and agile manufacturing, sustainable processing and finishing, digital manufacturing, robotics, 3D printing in manufacturing, AI and data analytics, need to be adopted and fine-tuned for the benefit of the industry.
Government support
Developed economies, the U.K. for example, are highlighting growth-oriented manufacturing as creative sectors by providing tax incentives and research support. In the context of textiles, advanced textiles are heavily research oriented and develop products where functionality occupies a front seat. So, this is, of necessity, a creative sector.
Following the pandemic, manufacturing related to national security, personal hygiene and medical products have received due attention among policy makers. Bipartisan support resulted in the CHIPS and Science Act signed into law by President Biden in August 2022. The act authorizes roughly $280 billion in new funding that not only boosts semiconductor manufacturing, but includes provisions to boost domestic research and manufacturing, as well, which will be beneficial to fiber-related sectors.
The Manufacturing USA program and support for collaborative research stands to offer meaningful help to our industry. This act’s line items include, among others, sustainable chemistry research and engineering biology, which will enable multidisciplinary approaches to develop sustainable raw materials and processes. This law has enabled the establishment of National Science Foundation Regional Innovation Engines (NSF Engines) which can receive support of up to $160 million in 10 years with initial funding for two years up to $15 million.
These engines are meant to spearhead collaborations among academia, businesses and community. In the case of textiles, the focus of the NSF Engine is on sustainability and has been awarded to the state of North Carolina, (the North Carolina Sustainable Textiles Innovation Engine).
India is a rising economic power, currently at fifth place in the world, according to the World Economic Forum. The textiles sector plays a vital role in employment and export earnings in India. The commodity textiles sector faces strong competition from China and Bangladesh, so as a way of diversification, India is investing in more advanced technical textiles, supporting a National Mission on Technical Textiles. Its aim is to boost research and development (R&D) in this sector, and provide both domestic and export marketing support, as well as skill development in advanced textiles.
It’s clear that a manufacturing revival is a favorable scenario for the technical textiles sector. Consumer-oriented functional textiles provide opportunities for SMEs to penetrate new markets and grow. As a case in point, Fredericksburg, Va.-based First Line Technology has taken the FiberTect dry wipe to decontaminate fentanyl, other synthetic opioids, and radiological particles.
Originally, this technology was meant for decontaminating mustard and toxic chemicals. Fine tuning technology enables us to create new markets beyond the original market, which can be accomplished by SMEs in the technical textiles sector, as is the case with First Line Technology.
Innovation engine examples
Multidisciplinary approaches that integrate different processes and engineering/scientific disciplines can add functionalities to textiles. Recently a team of researchers from the Massachusetts Institute of Technology (MIT) Media Lab, Electrical and Mechanical Engineering, and Architecture and Planning, developed an electronics-embedded textile structure. The comfortable and flexible fabric was knitted on a two-bed knitting machine. So far, commercially successful electronic textiles have been on single modality. This development is multimodal, capable of measuring temperature, heart rate and respiration level. The work was reported in npj Flexible Electronics.
Customized product development for medical and hygiene-related technical textiles can be accomplished by incorporating 3D printing and agile manufacturing. According to Dr. Jayanthi Parthasarathy, Manager 3D Printing, Nationwide Children’s Hospital, Columbus, Ohio, “3D Printing, additive manufacturing, or layer manufacturing is an evolving technology at the forefront of manufacturing processes. The advantage of the process is that it gives the ability to produce extremely complicated parts without design constraints and the need for expensive tooling.”
3D printing is well established in the medical sector. Medical textiles can be printed using biocompatible polymers on a customized basis. The advanced textiles sector needs to collaborate with healthcare systems in order to have deep roots in this field. According to Dr. Parthasarathy, “Since the process lends itself to low-volume production, or one-of-a-kind part production, it is extremely useful in making patients specific models and devices for single use.”
3D printing can be explored to develop customized automotive and aircraft parts using polymers. The margins for such high-tech and customized parts will be much higher than commodity parts. Although such product development activities may not be suitable for every SME, there are opportunities for those who are flexible and have invested in R&D.
Citing successes in the aerospace sector, Dr. Parthasarathy says, “Draco, the first hypergolic liquid rocket engine, was built by SpaceX and used in the Dragon Spacecraft. SpaceX has been using, testing and perfecting the 3D printing techniques for developing 3D printed flight hardware.” There is a need for more engagement of the advanced textiles community with the 3D printing community, which will enable innovative ideas and products for applications in aerospace, automotive and the home building industry.
Novel applications
Textile substrates can often be used in new, high-end applications by integrating techniques and principles from other disciplines. For example, a nanofiber battery separator is now an established application for submicron and nanofiber substrates, and fabric structures have been used as solar steam generators, achieved by fine tuning the yarn twist and tightness.
Woven fabric structures can also be constructed for continuous steam generation and scientific effects, like the “Maragoni effect” that enables salt rejection. This is the case with a recent study of a fabric woven with fine denier polypropylene and water repellent polyethene foam. This U.S. and China collaborative effort, reported in a recent issue of Advanced Functional Materials, enables desalination and clean water production.
Sustainability and circularity
The need to engage in sustainability practices is becoming more relevant as those engaged in manufacturing are expected to reduce greenhouse gas emissions. The industry must take global warming seriously; scientific studies and current data cannot be ignored. Recent data from the European Union’s Copernicus Climate Change Service reveal that February 2024 has been the warmest February since 1940. Data will push industries such as technical textiles to conserve energy and look for alternatives to fossil fuel-based raw materials wherever applicable.
Closed loop circularity and recycling techniques must be adopted by the textile industry if participants seek to develop value-added products. To make green technologies commercially viable, one must also be cognizant of the added cost. Therefore, cost benefit analysis and science-based data has to be made available to stakeholders and consumers.
Advanced circularity
Closed-loop circularity of textiles may yield rich dividends. At present, biodegradable textiles are the most ideal candidates for this process. AgResearch New Zealand has done pioneering work in this area and has found that recycled woolen carpets give nutrients back to soil while degrading, which ultimately results in greener pastures. This, in turn, enables healthier sheep, yielding high quality wool. This closed cycle is a classic example of advanced circularity.
In a similar vein, collaborative work between the Nonwovens and Advanced Materials Laboratory at Texas Tech University and India-based Jayalakshmi Textiles has resulted in the conversion of low-grade cotton into oil-absorbing mats. These mats with residual oil in them degrade over a time. Soil microbes digest the oil, yielding rich nutrients to the soil.
New products are also being developed from waste and recycled cotton. Professor Noureddine Abidi’s laboratory at Texas Tech University has developed biofilms from waste cotton, which can find applications in packaging and other products.
The advanced textiles sector is facing an opportune time when governments in countries worldwide are investing in manufacturing. Given the array of products that find high-tech applications, integrated approaches involving advanced manufacturing and sustainable processes must be evolved to develop cost-effective technical products. Such efforts will make advanced textile products commercially viable.
Dr. Seshadri Ramkumar is a professor in the Department of Environmental Toxicology and The Institute of Environmental and Human Health, Texas Tech University, and a regular contributor to Textile Technology Source.