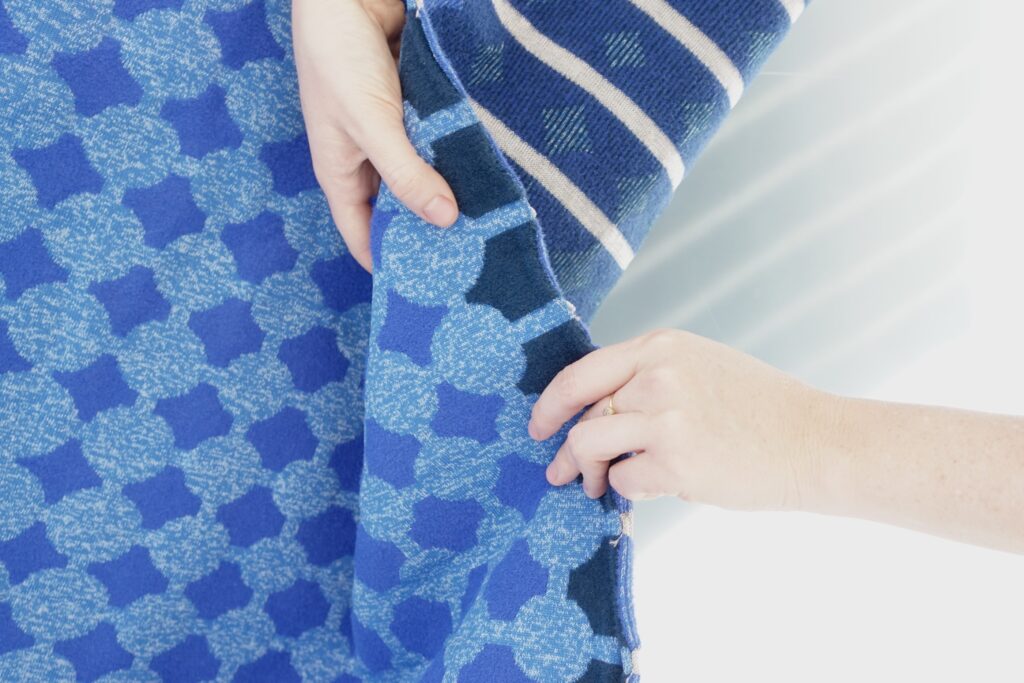
The smart fabric segment of the textile industry is poised to grow from $4.19 billion in 2024 to $15.21 billion by 2032, according to a Business Research Insights market report, but stumbling blocks remain that keep smart products from wider acceptance, and therefore even larger commercial success. The Advanced Textiles Association’s Emerging Textiles Conference in late September had several sessions addressing various aspects of the latest in smart fabric and e-textile research and development.
Transdisciplinary design
Gozde Goncu-Berk, associate professor in design at the University of California Davis addressed the health and wellness sector in her presentation titled “Empowering Health and Wellbeing: transdisciplinary design innovations in smart clothing and e-textiles.”
With the term “wearables” used to refer to all manner of smart garments and devices that work on the body, Goncu-Berk drew attention to an important distinction between accessories (such as watches and glasses) and items of clothing. The advantages of the latter—and the focus of her presentation—was that clothing is located physically close to the body, it is socially ubiquitous being worn almost all the time, and it covers a large surface area, all of which makes it well suited for complex data collection.
The central question posed was how can smart clothing contribute to the continuum of care across the entire health cycle? This came with a subtext questioning the role of design in achieving this. User-centered design is vital to the developing smart clothing that people will wear, and wear correctly.
Design, she argued, needs to be part of the whole process, working with each of the disciplines from the earliest stage possible. Interdisciplinary collaboration and teamwork are essential and something that she nurtures in her research and teaching at UCDavis illustrating where it has brought success through research projects in her lab.
Art and health
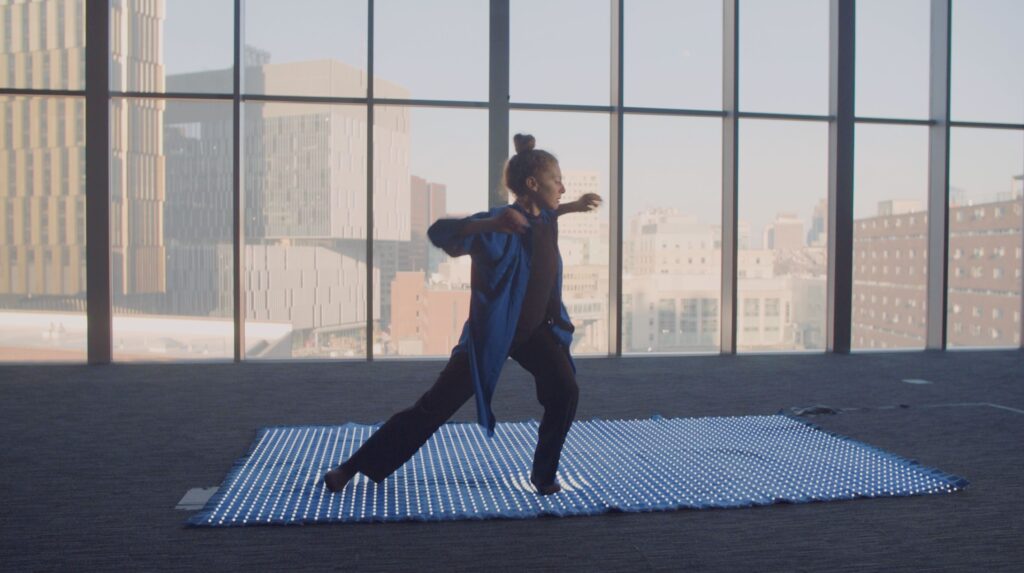
Scalability was one of the hot topics for smart textiles at this year’s ATA Expo, with an opening presentation from Irmandy Wicaksono titled “Textile microelectronics: architecting sensate and computational fabrics across scales” setting the pace. Wicaksono is a Research Affiliate in Responsive Environments at the MIT Media Lab.
His presentation reinforced the strong link between traditional textiles and e-textiles, a theme that has been present from the early days of wearable computing at the Media Lab. Included here were references to Javanese Batik, or Balinese Ikat, as well as Faig Ahmed’s Yahya al-Shirvani al Bakuvi, Melting Carpet, combining the digital with traditional textile culture.
In the speaker’s own Tapis Magique (with Haddad and Paradiso), a pressure-sensitive, knitted electronic textile carpet is used to generate 3D sensor data that is based on body postures and gestures. In the medical and well-being sectors, the technology is used to gather health data, but using an artistic approach here it drives an immersive sonic environment, merging new materials, sensing technologies and digital fabrication with contemporary dance and music in real-time, with the e-textile as interface.
Inspired by galactic space, 1,800 pressure-sensing pixels are embedded in the tapis’ geometric pattern. There are five layers to the fabric: The outermost is mink, luminous, high-flex polyester and melting yarns. Beneath this are the conductive yarns and high-flex polyester combined, followed by a multiplexing interface of hardware circuits. Next to this is a piezoresistive knit followed by a final high-flex polyester and melting yarns knit. The active area measures 4.5m squared.
The intention is to give dancers greater agency over their movements in an environment that is both physical and digital (“phygital”), with the music directed by a dancer’s movement as the sensor data is mapped onto MIDI streams triggering the soundscape—an inversion of the conventional choreographic process.
Collaborative problem solving
The Eeonyx Corp. makes smart fabrics for the Internet of Things (IoT) with an ISO 9001:2015 Certification for Quality Management and Quality Management Systems (QMS). Presenting for the company, Dr. Nic J. Brownless’, Ctext FTI, discussed “Challenges in making the ideal sensor fabric.”
Communication is at the heart of the problem, and better communication is also the solution, according to Brownless. “Textile technologists are not electrical engineers, and electrical engineers are not textile technologists. We don’t always understand each other,” he says.
For an SME fabric-coating company making pressure sensing fabrics, this is a challenge, as it relates to their ability to properly understand the performance requirements, customer needs, the location of conductive media within a coated conductive fabric, and its subsequent impact on performance.
Brownless’ presentation described the practical challenges in gathering information needed to provide the right product and understand the limitations concerning what can be done, as well as what cannot be done and why. While questions around laundering might be anticipated, some of the other sample questions for a client were less obvious, such as:
- What is the level of durability required and how is it measured?
- Will the hardware be located on one side of the fabric or both sides?
- Will the fabric be encased in the final product?
The answers, however, still might not provide clarity, so he suggests sending the customer a sample fabric, knowing that it’s not going to work. The customer is then asked to tell him what’s wrong with it, which Brownless says will bring his company closer to a fabric that will meet the customer’s requirements.
Part of the issue is that testing for fabrics is flawed and inherently inaccurate, but “It’s what we’ve got,” he says. For example, using a probe to test surface resistance, but fabrics are not equal all over the surface, and the probe itself was designed for film. Customers want linear behavior in resistance performance, he says, but “there’s nothing linear in fabrics, except that they’re sold by the yard.”
So, taking a regular textile and coating it with conductive material, “how do you make it an ideal sensor fabric?” he asks. The answer is complex and involves considering everything in the base fabric from fiber to yarn, structure, density or thickness, and its finish, as well as the manufacturing process. Decisions regarding the conductive component require considering “what, where, how, how much and post treatment.”
Vertical flexible interconnects
Ph.D. candidate Prateeti Ugale, Wilson College of Textiles, NCSU, discussed the use of vertical flexible interconnects for e-textiles in her presentation. Her advisor, Dr. Amanda Mills, NCSU, is part of the team pursuing this research.
Ugale says there is growth in the e-textiles market in part because of their practical uses in healthcare, where e-textiles offer a unique combination of convenience, real-time data analysis and personalization of medical treatments. She’s been investigating how to improve e-textiles in this market with textile vertical interconnects.
Vertical Interconnect Access (VIA) is an essential component of a printed circuit board (PCB) that creates electrical connections between different PCB layers. “We do see a lot of vertical interconnects in e-textiles,” she says. But they aren’t necessarily textile VIs.
She has been working on a means to imbed VI in textiles using conductive ink applied with screen printing. The wearable textile sensor is held between a TPU backing and encapsulation that provides protection against dirt, water and other impurities; heat dissipation from high power components; and mechanical durability.
The advantage of a vertical interconnect is its 3D integration, which allows more compact and integrated designs with electronic components on the front and back. Textile VIs can also offer secure communication systems using complex circuitry that can be packed into a smaller footprint, and they remove hard surface components, such as snaps or rivets, to avoid soft-to-hard connection stresses.
As her work continues, she’ll focus specifically on integrating textile vertical interconnects into electromyography (EMG) monitoring wearables, which can offer an EMG procedure a less invasive approach with on-skin sensors. The research team believes that vertical interconnects and connectors for wearable e-textiles are a crucial step towards fully integrated, flexible and functional wearable electronics.
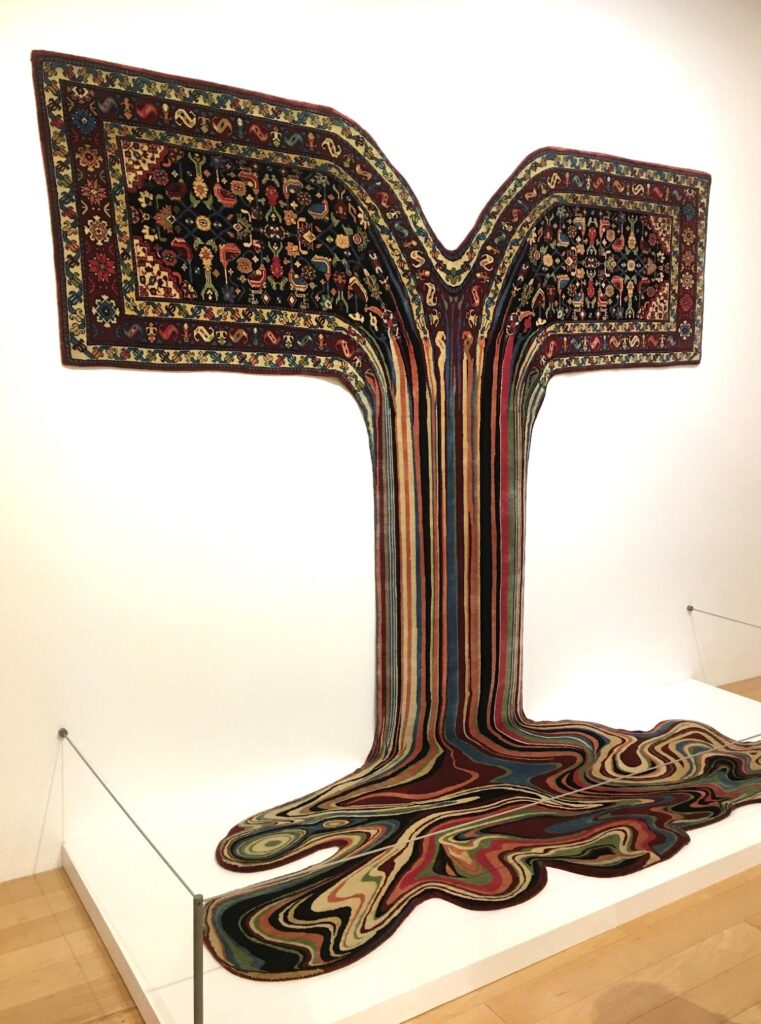
Dr. Marie O’Mahony is an industry consultant, author and academic based in London.
Janet Preus is senior editor of Textile Technology Source, a publication of the Advanced Textiles Association. She can be reached at janet.preus@textiles.org.