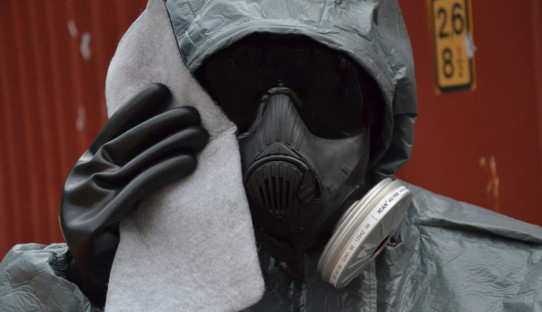
“Applied research deserves Nobel prizes,” proclaimed the editorial of Nature Materials in January 2010. Although, the Nobels are known to be rewarded only to basic discoveries, there are plenty of examples to showcase rewarding research of applied nature—for example, the 2014 award in Physics for blue light LEDs. More and more, academia is emphasizing translational research—research that leads to commercialization within a short period of time. There are many factors that are contributing to this mindset, such as a lack of federal dollars for a large number of principal investigator-initiated research, and the increase in industry collaboration and other economic incentives to the inventors.
Very recently, US academia, particularly in science and engineering disciplines is endeavoring to reward such translational research by counting such translational efforts towards tenure and promotions, and recognizing these achievements with awards. Although “publish or perish” is still the guiding mantra in academia, commercialization aspects are getting some attraction due to a variety of rewards for the institution (and individual researchers), such as royalty returns.
A success story
The research carried out at Texas Tech University’s Nonwovens & Advanced Materials Laboratory has been focused on this aspect since the year 2000 and has had success with the invention of “FiberTect®,” a dry decontamination wipe.
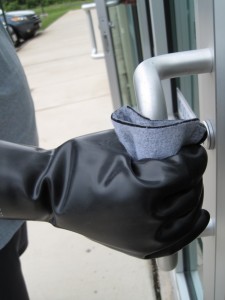
FiberTect is a classic example of mission- linked research, which has both basic and applied aspects intertwined together. The FiberTect story showcases how an academic laboratory, when it is able to work on a project that’s deemed to be an immediate requirement by a customer, can develop a commercial product. In this case, the customer is the U.S. Department of Defense.
As it goes in every field, timing also plays an important factor in success. The genesis of FiberTect is worthy to know as the research and development endeavor coincided with the time when the U.S. and the other NATO partners focus on fighting terrorism right after the 9/11 attacks.
Again, as long as a research activity tackles a problem that is an immediate priority for a particular customer and delivers the required product at the adequate price point, it can be a commercial success. In our opinion, FiberTect fits these criteria.
How it happened
About 1998, based on the input and advice from Admiral Elmo R. Zumwalt, Jr., Texas Tech University started a research program to focus on countermeasures to chemical and biological threats. Research projects focusing on four important aspects of chemical and biological countermeasures evolved: Sensing, Shaping, Shielding and Sustaining.
As the multidisciplinary program focused on the requirements of the U.S. Department of Defense, funding was secured and continued for a period of twelve years since the year 2000. FiberTect has its origin in this program and the project materialized to the commercial stage (“mind to market”) within a decade.
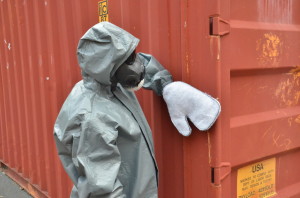
The development of a non-particulate and non-corrosive sorbent material for decontaminating personnel and military equipment is considered an important requirement for the modernization strategy in the decontamination technology by the U.S. Department of Defense, as stated in its 2005 and 2006 annual report to the U.S. Congress. The research at Texas Tech University exactly fit this requirement, producing a dry sorbent technology in the mid-2000.
Although catalysts and other particulate technologies such as metal oxides are extremely capable of decontaminating nerve agents and toxins, their particulate or loose powdery nature deters them from a wide range of applications. For example, a warfighter may not feel comfortable with aqueous liquids like bleach or loose powders in certain areas of the body, and so they may not be suitable in all situations. Since FiberTect is a dry and non-solvent based technology, it could find applications where other technologies were not appropriate.
Texas Tech University focused on the development of dry sorbent using a well-established nonwoven technology: needlepunching. A “sandwich” concept was adopted to develop a three-layered absorbent and adsorbent wipe, for which a patent was obtained in 2009. The top and the bottom absorbent layers easily wick away the volatile toxins in the liquid form, while the middle adsorbent carbon will be able to hold-off the volatile vapors that are emanating from the toxins. More importantly, the middle adsorbent carbon is in the non-particulate nonwoven form, which is an essential DOD requirement.
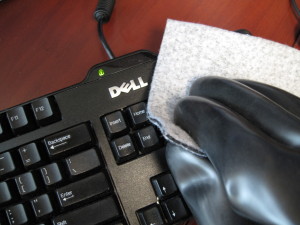
Additionally, the three-layered composite is a nonwoven, whose porosity is higher than the woven composites. Furthermore, as the structure is needlepunched, it is convenient to clean into the nooks and crannies of the contaminated objects.
Collaboration with Lawrence Livermore National Laboratory proved that this dry wipe technology is a better candidate when tested with mustard gas, and it was recommended as an important component to the “Low Cost Personal Decontamination System” (LPDS).
Market entry
FiberTect dry wipe is manufactured by Waco, Texas-based Hobbs Bonded Fibers, a leading needlepuncher in the country. In 2010, FiberTect wipe made its presence in the commercial space due to the efforts of Chantilly, Va.-based First Line Tech LLC, a member of IFAI. FiberTect is marketed to several agencies, including some government clients.
The model of this research, which is a clear example of mission-linked research, has been recognized by the American Chemical Society as a good example for the federal role in supporting innovation and translational research.
When the technology has multiple applications, i.e., platform technology, its commercialization success is enhanced. As it’s a porous sorbent, the product could also be used in oil and utility industries to tackle volatile oil spills and volatile organic vapors. It showcases an industry-relevant research, whose basis is in fundamental R&D. These days, the wave is behind translational multidisciplinary efforts that can develop entrepreneurs and create jobs. FiberTect illustrates how successful this model can be.
Prof. Seshadri Ramkumar’s work is in nonwovens and technical textiles with the Nonwovens & Advanced Materials Laboratory, Texas Tech University, Lubbock, USA.
Photos and video: First Line Technology