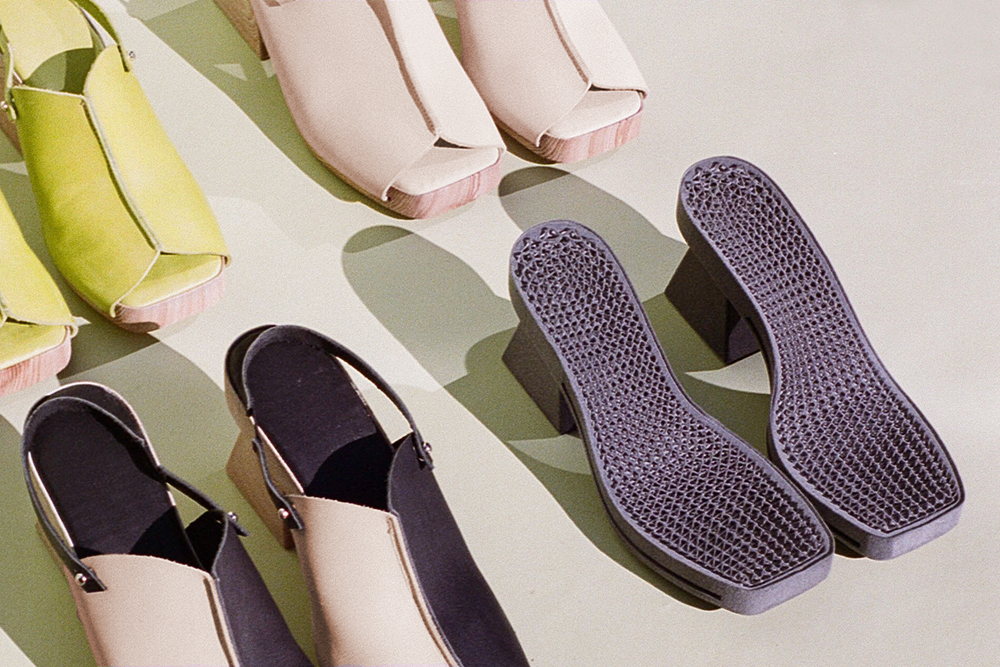
3D printing, or additive manufacturing, can reduce the greenhouse gas emissions of footwear manufacturing by some 48 percent, and reduce water consumption by 99 percent, compared with traditional footwear manufacturing, according to a study led by Portland, Oregon’s HILOS, in partnership with Yale’s Center for Business and Environment.
Hilos’ circular product platform enables footwear brands to launch 3D-printed lines without inventory or waste. They also offer their own concept-design mules, clogs, and sandals made out of thermoplastic polyurethane (TPU) in partnership with 3D printer GKN Additive. Their process not only cuts down on glue but reduces the number of steps (and hence labor costs) in manufacturing, and that makes the shoes easier to disassemble for recycling at end-of-life.
CEO and co-founder Elias Stahl Elias says, “Today’s revolution in materials, 3D-printing, and AI-driven design provide an historic opportunity to reinvent global supply chains for an on-demand, zero-waste future. Instead of being an industry built around where to make, we can become one focused on how to make, so shoes can be made anywhere, locally, and sustainably.”
Hilos recently raised $5 million in a funding round, with investment from Eric Sprunk, the former COO of NIKE, alongside other NIKE executives.
Adidas’ work with CARBON, a Silicon Valley-based tech company, on its FUTURECRAFT line of 3D printed shoes, is also moving the sustainability needle. Adidas newest FUTURECRAFT 4DFWD running shoes features Carbon’s new partially bio-based resin, EPU44, 40% derived from plants.
Carbon’s Digital Light Synthesis technology polymerizes the printed resin using light, creating lattice-like structures perfect for the soles of running shoes and other sports equipment.