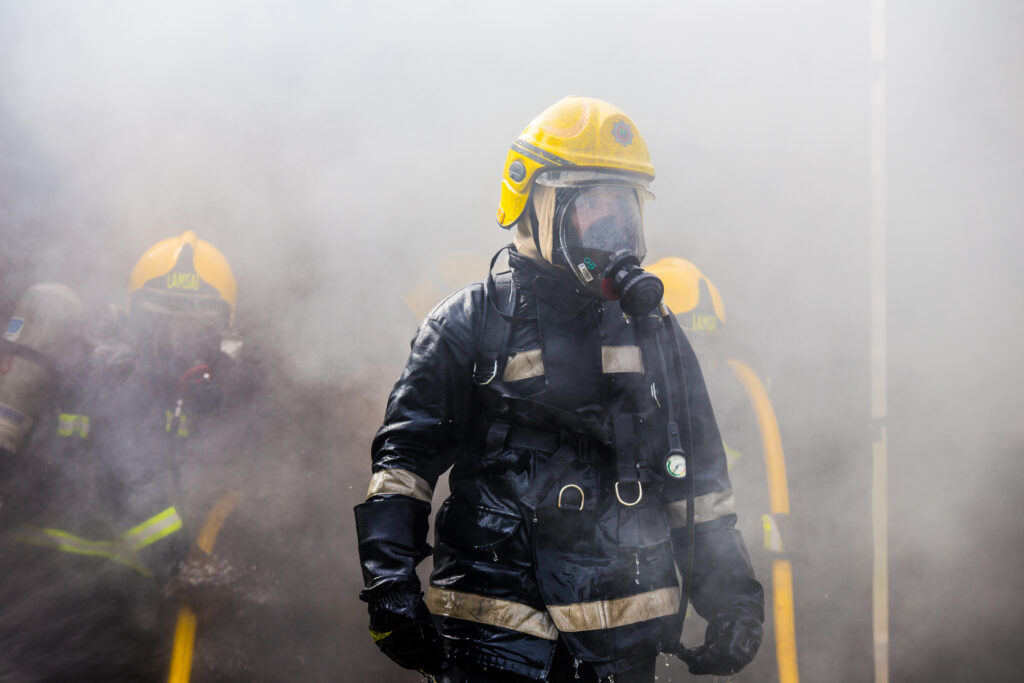
The textiles sector is feeling the pressure of low demand and higher costs due to global inflation and geopolitical circumstances. A survey undertaken among 250 participants in a recent meeting organized by the Texas Cotton Association revealed that the demand for non-essentials like textiles is low, and the imports to the U.S. and other developed economies will pick up during the second quarter of 2024.
What does this survey reveal? Demand for textiles will depend on the economy and therefore the industry must follow a systematic approach in delivering products at a competitive price that will cater to the requirements of the global market. The 2PS approach—Products (P) and Processes (P) as a System (S)—offers a sensible path to deal with uncertainties.
While the commodity textiles sector may not spearhead the growth of the industry soon, there are certainly opportunities for textiles in protective and defense markets, health, hygiene, and also environmental protection. New developments can be accomplished if the industry follows a products and process systems approach. Among the immediate market segments for this approach are sportswear, military clothing, agrotextiles and geotextiles.
Chem-bio defense textiles
The chemical and biological protective textiles sector is particularly suited for adopting the systems approach. As approval for new medicines through the U.S. Food and Drug Administration is a time- and money-consuming process, getting regulatory clearance and approval for defense applications are also complex. A collaborative and systems approach can be a useful pathway.
Major agencies, such as the Defense Advanced Research Projects Agency (DARPA) and the Biomedical Advanced Research and Development Authority (BARDA), are involved in such approvals and play vital roles in initiating and funding projects. More frequently these agencies are looking at systems approaches to find solutions to tackle complex threat situations, including chemical attacks, pandemics and biological warfare scenarios.
Given the complex challenges in handling toxic chemicals belonging to different classes (blister agents, nerve gas, toxic industrial chemicals and others), simply using a high surface area adsorptive substrate may not be a panacea. The U.S. Army Natick Soldier Systems Center has been at the forefront in research to develop a universal PPE substrate to tackle chemical and biological agents using the systems approach. Even though this is a tall challenge, the effort is much needed and will move the research forward in CBRN (chemical, biological, radiological, nuclear) defense.
The center’s name itself highlights the importance of the systems approach for developing next-generation military technologies. For example, the systems approach would utilize a lightweight, adsorptive, protective substrate (such as non-particulate, high surface area, activated carbon) to adsorb volatile toxins, and functional compounds added to the substrate would help to neutralize toxic agents.
Research is ongoing to utilize metal oxides and other compounds to give multiple functionalities to fabrics. The Metal Organic Framework approach is also being investigated in a few academic and research laboratories, which can be used in next generation defense technologies.
A real-world example
The systems approach has seen commercial success in the chemical decontamination arena to clean and wipe toxic chemicals and synthetic opioids. In addition to defense sectors, such decontamination products also find applications in safety markets, including emergency medical services, police, firefighting and crime scene investigating.
Hybrid decontamination systems involving chemicals and nonwoven products are used to enhance the efficiency of bulk cleaning. One approved system uses a chemical formulation which consists of a micro emulsifier and an oxidizer to neutralize toxic chemicals.
The decontamination system approach involves firstly wiping the contaminated area with a high surface area nonwoven wipe followed by the spraying of a chemical. Finally, the contaminated surface is again wiped using a dry wipe enabling a highly efficient hybrid decontamination approach. The technology is a combinatorial method, but it is also interesting to note that the project itself is a systems approach involving the federal government, academia and small-scale industry.
Participants and approaches
The advanced textiles sector lends itself well to small- and medium-scale enterprises (SMEs), which are nimble and hence have freedom to take a “detour,” if necessary, to enable timely success. These companies are better suited to adopt systems and combinatorial approaches involving different fields and multiple entities towards successful commercialization.
There are opportunities to avail funding for such projects from the federal government through multiple agencies such as the U.S. Dept. of Defense (DoD), National Science Foundation (NSF), Dept. of Agriculture (USDA), and Dept. of Energy (DOE).
Global initiatives are also significant, as other countries are also encouraging translational projects that can result in startups and job creations. For example, as the U.S. NSF has the Innovation Corps (I-Corps) Initiative, India has Start-up India Programs. These programs encourage collaborative efforts, where systems approaches can yield results. In textiles, projects need to involve machinery makers, fiber producers and product developers, who work together to think through the projects as a system to contain costs, conserve energy and deliver final products at competitive prices.
The international industry
C. K. Wong, Chairman and CEO of Hong Kong-based U.S. Pacific Nonwovens, an advanced textile industry participant for 53 years, advocates for new approaches that can take existing fibers and processes to develop value-added products. Cotton can find new opportunities in the nonwovens sector, as the cost will be competitive with bioplastics, adds Mr. Wong. The industry has been successful in developing food packaging and medical products using bio-based materials, such as the thermoplastic polyester PLA.
Japanese multinational chemical company Asahi Kasei Corp. has been leading in the development of spunbond nonwovens using cotton linters to develop products for the wipes and cosmetics industry.
Consumers like green products but expect products with good functionality at similar cost levels as synthetic-based nonwovens, which is a challenge for the industry. “The nonwoven industry is transitioning to less plastic-based raw materials,” says Tom Carlyle, Nonwovens Commercial Manager-Americas at Lenzing Fibers. “Consumers are becoming curious about resources, which will drive innovation. Furthermore, growing regulations, such as the EU Single-Use Plastic Directive, will necessitate the immediate need.”
“Spunlace [hydroentangling] technology is employed in China to develop virgin cotton-based nonwovens with 6 or more lines running,” says Oliver Doring, director of sales and marketing at Trutzschler Nonwovens, headquartered in Germany. Two spunlace lines are developing cotton-based spunlace nonwovens in India and an additional line will be online soon which can develop cotton-based wipes.
These are some of the examples of products and processes working as a system to improve lifestyles. But the industry must be always watchful of the cost of the product if it has to be a commercially viable one.
The private sector and industry groups in the textiles and fiber fields support applied projects that will have quick return on investments. The 2PS approach will be beneficial to handle industry supported projects. U.S. cotton growers through Cotton Inc. are supporting many projects that have yielded commercial successes.
One approach has resulted in developing a cotton technology that has faster wicking cotton to keep the skin dry while maintaining the comfort properties of cotton. Similarly, efforts in Australia through Australian Wool Innovation are enabling new products from wool which becomes a part of a larger system involving other fibers with high-tech applications.
Sustainability and a systems approach
Many countries world-wide are committed to reducing the use of fossil fuels, as well as products made from fossil fuels. To reach net zero carbon goals by 2030, new approaches and methods are needed for the manufacturing sector to develop environmentally friendly products. Here again, the 2PS approach could be useful.
Already, the regenerative cellulosic fiber segment of the industry, for example, is adopting the systems approach to involve forestry, agronomy and textile manufacturing to manufacture fibers from pulp and other natural resources. Even in the synthetic fiber industry, the efforts are ongoing to develop chemical and mechanical regeneration and recovery methods.
New partnerships are emerging between different industries such as fiber, paper, plastic, and automobiles, which employ multiple synergies to solve complex problems. Recently, Japan-based Toray Industries Inc., announced an agreement with Honda Motor Co. Ltd. to develop polymer recycling technology to recycle glass fiber reinforced Nylon-6 car parts to a basic monomer such as caprolactam.
The technology uses subcritical water, which is water at higher temperature and higher pressure with superior dissolving power. The systems approach in this effort involves companies belonging to different sectors, which uses emerging technology to develop environmentally friendly products with a greener process.
The systems approach involving synthetic biology, material science and the polymer industry is interesting to observe. California-based Mi Terro engages in this approach with the goal of eliminating microplastic pollution by replacing plastics with sustainable and durable bio-based materials. The company is collaborating with American pulp and paper company, Georgia Pacific, in developing a biobased coating for paper packaging material that will have good resistance against water, oil and grease. Such biobased chemical formulations are needed due to growing regulations, such as the phasing out of PFAS compounds.
The systems approach is a new pathway for the industry to develop new products at a competitive price. In addition to using multiple products and processes as a package to tackle a problem, this approach also includes different areas of expertise in science and technology, marketing and communication so that industries are successful.
Dr. Seshadri Ramkumar, Ph.D., is a professor at Texas Tech University, Lubbock, and a frequent contributor to Textile Technology Source.