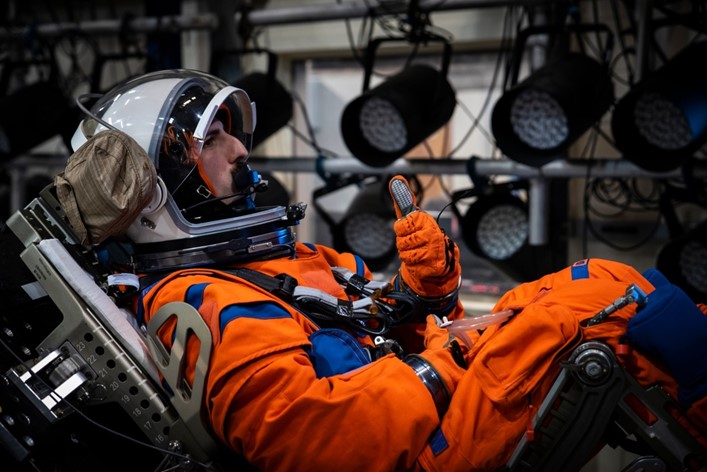
Testing with human volunteer subjects began in October 2023 at Wright-Patterson Air Force Base in collaboration with the Air Force Research Laboratory (AFRL) engineers. The goal has been to evaluate the latest version of astronaut crew seats and flight suits intended for the Orion spacecraft.
Conducting human tests enabled the team to collect safety data and receive continuous feedback from the participants, addressing concerns about suit fit, comfort and seat integration during impact events. These tests were performed at impact levels expected during capsule reentry and landing, reflecting more typical experiences.
“Artemis II will be the first operational test of the Orion suit and Orion seat with human occupants,” says Chris Perry, senior biomedical engineer, Biodynamics Section, 711th Human Performance Wing. The Artemis II mission is tentatively scheduled for September 2025.
Using test dummies, the team could capture intricate metrics encompassing various accelerations, forces and moments, says Dustin Gohmert, Orion crew survival engineer at NASA. But to assess comfort or pinpoint areas for minor adjustments, human testing remains essential before the suit can be employed in an actual mission. This testing had three primary objectives:
- To guarantee that the placement of a diverse range of human participants in the seat doesn’t disrupt the restraint system, headrest or equipment during acceleration exposures.
- To confirm that the interaction between the suit and individuals doesn’t lead to hotspots or soft-tissue injuries during horizontal and vertical impacts.
- To ensure that all participants could brace appropriately in a neutral posture during horizontal and vertical impacts, with their heads against the headrest and shoulders against the seatback.
“The human occupant conforms to a suit and the seat in a way the ATD (test dummy) cannot and still provides measured accelerations, which can be used to evaluate safety,” Perry says. “They also can provide a verbal assessment post-test to address the goals.”
Apart from the horizontal tests, the human subjects were also subjected to controlled vertical impact simulations, replicating predictable landing scenarios. The vertical drop tower replicated the horizontal test’s context, yet it allowed for adjusting the seat orientation concerning how the body is pre-loaded, Gohmert said.
The issue lies in aligning with gravity: human positioning in the vehicle, considering the landing acceleration vector, results in a discrepancy in the force of gravity experienced in our testing setup. “For example, in some of these cases, we’d actually be hanging out of the seat belts,” Gohmert added. “Well, that biases you already away from the seat, which could exacerbate the response. But, on the drop tower, we’re going to actually be laying in the seat and just fall into it, and it really mimics the perfect Orion landing, as we ‘fall on the drop tower to the controlled deceleration.’”
Gohmert said the team was able to match the exact descent seen in Artemis I, which was “the perfect landing,” something he hopes to see in all future landings.