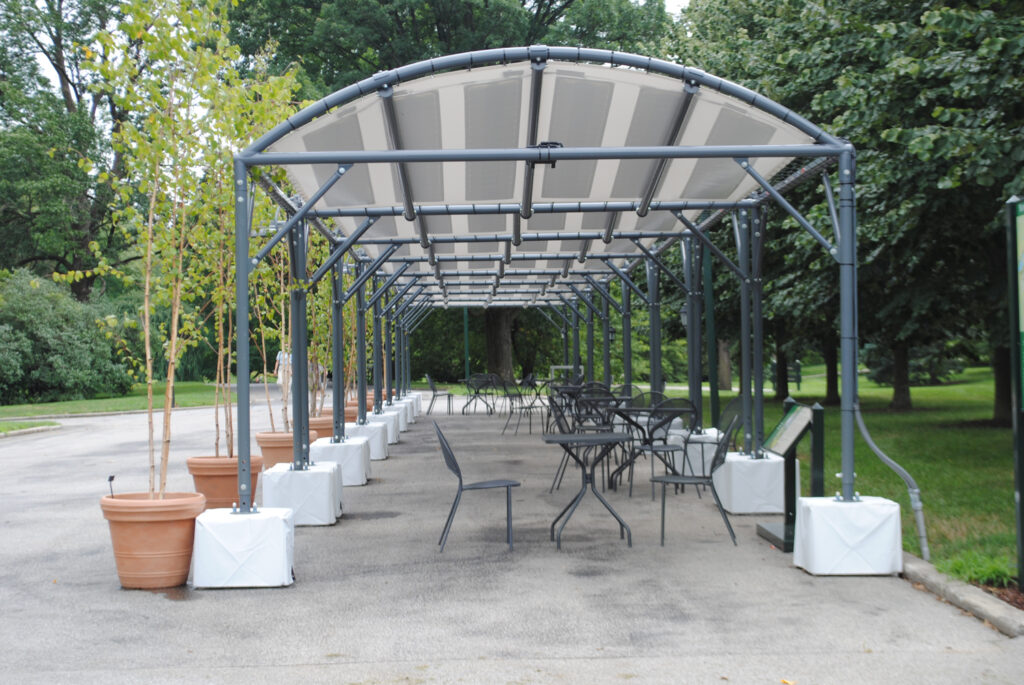
According to the International Energy Agency (IEA), the amount of renewable capacity added to energy systems around the world grew by 50 percent in 2023, reaching almost 510 gigawatts (GW), with solar PV accounting for three-quarters of additions worldwide.
The IEA forecasts that U.S. solar power generation will grow 75 percent from 163 billion kilowatt hours (kWh) in 2023 to 286 billion kWh in 2025. They also expect that wind power generation will grow 11 percent from 430 billion kWh in 2023 to 476 billion kWh in 2025. Hydrogen power and sustainable aviation fuel (SAF) are also poised for growth.
The economic opportunities provided by the generation of alternative energy, requiring new facilities, new materials and a wide range of feedstocks, could likewise fuel the growth of innovative and technical textiles. Seen and unseen, these critical components include unique polymers, composites, membranes and filters, as well as performance textiles for wind and solar that are lighter, stronger and often recyclable.
From solar cells to solar fabric
Recent developments in light weight, super-thin, flexible photovoltaics have enabled the solarization of fabrics, expanding the potential range of energy-producing form factors. Brooklyn-grown Pvilion laminates their solar cells to a variety of textiles to create a range of canopies, tents, curtains, building façades backpacks and clothing. “Once you have the panel, you can turn it into anything,” says Colin Touhey, the company’s co-founder and CEO.
Pvilion’s advantage is in its systems that provide both shelter and power in one structure to partners such as Carnegie Hall, Bloomberg, Tishman Speyer, The City of New York, Yale University, the U.S. Air Force, the Florida Dept. of Transportation and The City of Miami.
“Solar fabrics are getting better and better,” Touhey says. He explains that the company is agnostic regarding substrates, focusing instead on durability and longevity. Pvilion creates solar fabrics from rip-stop nylon, PVC-coated polyester, PTFE-coated fiberglass, Dyneema, and perhaps stretch substrates. “We care about quality,” he continues, pointing out that it is critical for Pvilion’s projects for the U.S. military, which also requires fabrics to be made in the U.S.
“We are more and more trying to build a line of finished product, as mass production is the goal for price,” says Colin. “But we are happy to work with people who have small volume. Being a solar power company doesn’t mean anything if it doesn’t fit into the customer’s requirements.”
From sails to wind turbines
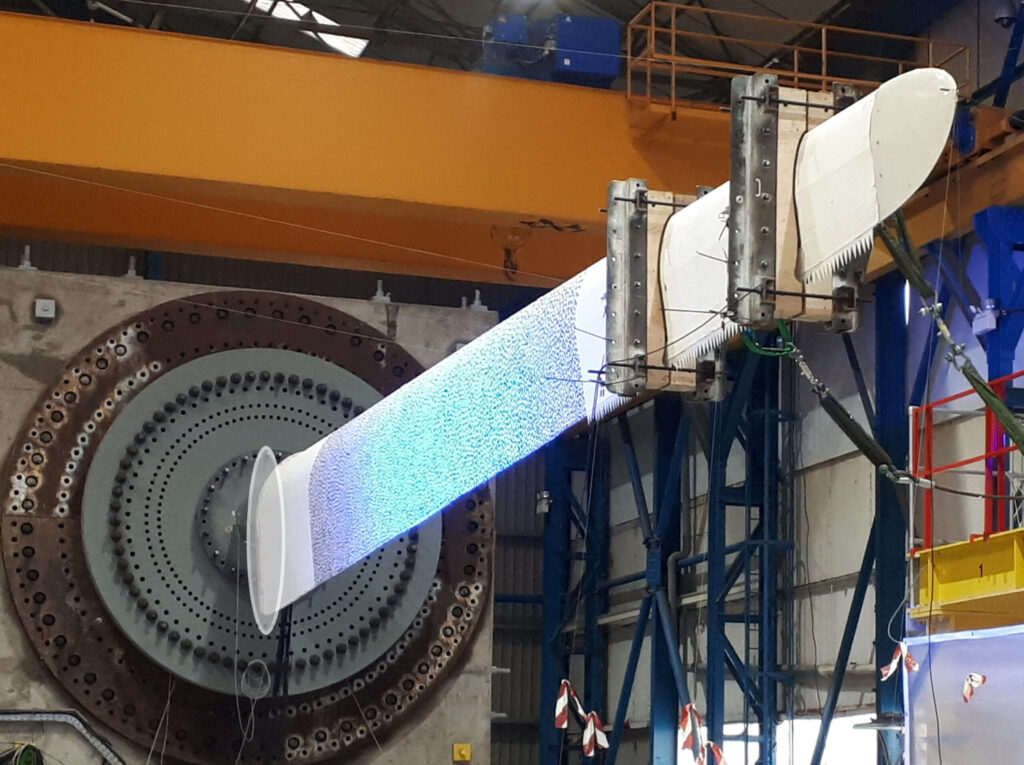
A Scottish start-up called ACT Blade is revolutionizing wind power with an innovative fabric and specialized modular manufacturing system for turbine blades.
The new blades are longer in length without increased weight, and comprise fewer materials and simpler, streamlined production methods. They feature a slender supporting structure made from a composite material that is completely covered by the technical textile.
The protective outer shell for the wind turbine blades was manufactured by Concordia Textiles Group, based in Belgium. The fabric is reparable and is composed of elements that can be easily separated for recycling at end of life.
According to Rik Gekiere, Concordia’s sales and product manager, “We developed a laminate that is the common denominator of more than twenty technical requirements, by combining the strength and elasticity of a fabric with a protective layer. Rain erosion resistance and durability over time were the most challenging to achieve. We prefer to wait to provide more details of the product until the actual market release of the blades.”
ENEL Green Power S.p.A., an Italian multinational renewable energy corporation, is partnering with ACT Blade to develop the project.

A wind technology called OceanWings®, developed by VPLP Design in France, is said to enable a 45 percent savings in fuel consumption and a subsequent reduction in CO2e for sailing vessels. The vertical windsails provide aerodynamic lift and feature automated positioning to maximize thrust.
OceanWings are made from eco-composites that include linen fiber and recycled thermoplastic resins. The outer bag is 1000 denier nylon, with a layer of urethane to protect against punctures and abrasion.
The sails were first trialed in 2019 on the Energy Observer, an experimental vessel designed to test alternative energy sources in maritime conditions. In 2022 the commercial wind-powered cargo ship, the Canopeé, launched with four OceanWings that reduce fuel consumption by up to 42 percent in good weather conditions.
Green hydrogen: fuel of the future?
The World Economic Forum defines green hydrogen (H2) as hydrogen produced through electrolysis, usingrenewable electricity from solar or wind to split water into two hydrogen atoms and one oxygen atom. Green hydrogen can be used to decarbonize transportation, including heavy trucks, aviation and shipping, as well as in the manufacturing of steel, cement and other hard-to-abate industries.
At the heart of the green hydrogen process are proton exchange membranes, or PEMs. These membranes play a vital role in H2 production, fuel cells, and flow batteries for energy storage. The Chemours™Company, based in Wilmington, Delaware, dominates this market with their Nafion™ brand portfolio of membranes, dispersions, and resins.
Nafion is a synthetic polymer with unique ionic properties, created by incorporating perfluorovinyl ether groups terminated with sulfonate groups onto a tetrafluoroethylene (PTFE) backbone. The resulting product is a thermoplastic that can be extruded or solution-cast into films for composite membranes.
In response to a request for information, Nafion portfolio’s product manager referred to a paper published by Chemours’ technical team: “Advancements in Thin, Reinforced Proton Exchange Membranes for Water Electrolysis” by Ryan Gebhardt, et al.
“Employing a thinner and mechanically supported membrane can enhance both the electrochemical performance and mechanical properties. With the demand for cheaper hydrogen, these new membrane designs are needed to achieve advanced performance metrics,” it says.
While the green hydrogen economy is still in its infancy, the U.S. Dept. of Energy (DOE) recently announced $750 million, funded by the 2022 Bipartisan Infrastructure Law, for 52 projects across 24 states to reduce the cost of clean hydrogen. According to the DOE, clean hydrogen is set to play a vital role in reducing emissions from the most energy-intensive and polluting sectors of the economy.
For example, Airbus is testing the use of hydrogen fuel cells to generate electricity to power aircraft that fly with almost zero emissions. Airbus’ ZEROe project hopes to bring the world’s first hydrogen-powered commercial aircraft to market by 2035. Flight testing of the fuel cell propulsion system on an Airbus 380 is scheduled for 2026.
Decarbonizing aviation with SAF
The airline industry uses about 20 billion gallons of jet fuel every year, and globally aviation accounts for 2 percent of all CO2e and 12 percent of CO2e from transportation, according to the DOE.
Sustainable aviation fuel (SAF) reduces emissions from air transportation, and when blended with conventional aviation fuel is a drop-in for today’s aircraft and infrastructure. Depending on the feedstock and blend, SAF can reduce aviation’s CO2e by up to 80 percent.
There are several pathways to making SAF, based on various feedstocks. These include sustainably sourced renewable waste such as cooking oil and animal fat; biomass, such as agricultural and forest wastes and solid municipal waste; and power-to-liquid SAF made from captured CO2.
“Sustainable Energy Generation from Textile Biowaste and Its Challenges,” a paper by Khandaker, et al., Dept. of Textile Engineering, Dhaka University of Engineering & Technology, Bangladesh, reports that waste from the textile industry could also be a significant source of biomass for fuel.
LanzaJet, a sustainable fuels technology company spun out of LanzaTech in 2020, produces ethanol alcohol-to-jet SAF from any source of low-carbon ethanol, including biomass, industrial waste, municipal solid waste (MSW), and CO2. The company’s recently opened Freedom Pines facility in Soperton, Georgia, supported by DOE’s Bioenergy Technology Office (BETO), will produce nine million gallons of SAF and one million gallons of renewable diesel in its first year of operations.
LanzaJet and Tadweer, (Abu Dhabi Waste Management Company) are cooperating in a feasibility study to initiate SAF production from municipal and commercial solid waste. The hope is that up to 350,000 metric tons of hard-to-recycle municipal and commercial solid waste can be transformed into 200,000 metric tons of ethanol per year.
Tadweer’s facility will transform solid waste streams into a synthesis gas consisting of CO, CO2 and H2, via a gasification unit licensed by sustainable technology solutions provider NextChem, part of MAIRE Group. The gas stream is then transformed by LanzaTech’s microbe-powered bioreactor into CarbonSmart™ ethanol, which LanzaJet can then convert to SAF.
Renewable energy is a growth industry, accounting for 90 percent of all new electricity installed each year, worldwide. While it’s early days, there are opportunities for the textile industry to be involved.
A battery in a balloon
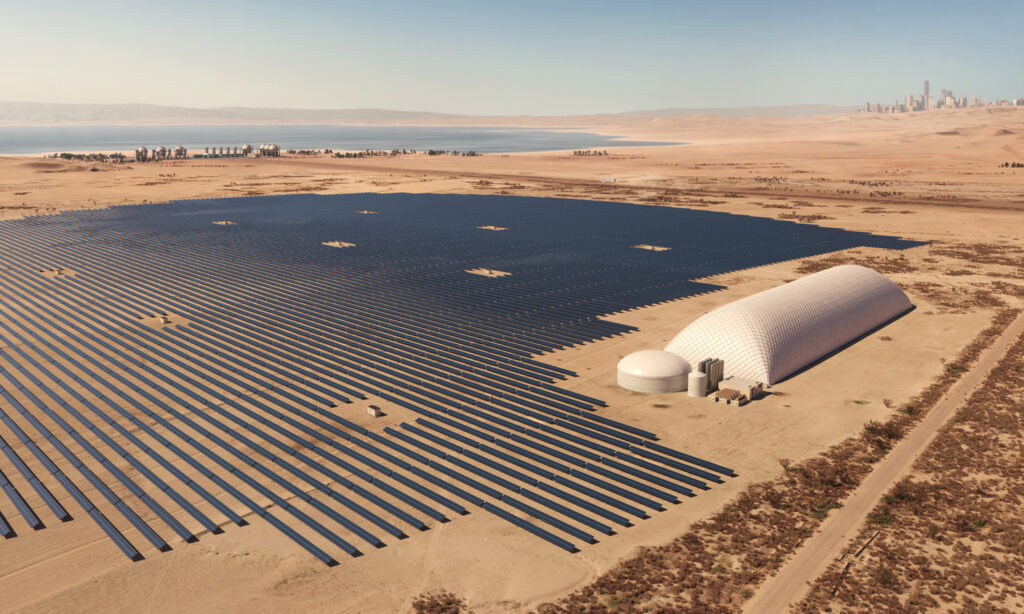
A company called Energy Dome, based in Milan, has developed a thermodynamic method of long-duration energy storage in a “battery” that uses CO2 stored in a huge fabric dome, like a balloon, made of PVC-coated polyester.
Energy from a local grid or nearby solar farm compresses the CO2 into a liquid during the day. At night, the liquid CO2 expands back into gas, driving a turbine that produces electricity and sending it back to the grid.
Energy Dome already has its first US installation planned for 2026 in Columbia County, Wisconsin, with Alliant Energy, and it has recently opened an office in Boston with a “growing ambition to decarbonize the world with our CO2 Battery™ technology.”
Debra Cobb is a freelance writer based in North Carolin with special expertise in the textile industry. She is a frequent contributor to Textile Technology Source.