A range of new materials and technologies are adding functionalities to textiles.
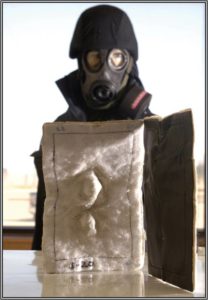
Textiles are well established as passive materials offering comfort and protection, as well as design and fashion choices. With strong interest in promoting textile manufacturing and enhancing the utility and performance of textiles, efforts have been initiated by academia and government researchers to enable them to be active. Textiles that can provide functional performance properties, making them active, are generally termed “smart.”
The defense market sector has been an early supporter and initiator of developmental initiatives to integrate high performance and functional properties into textiles. The Military’s Joint Service Lightweight Integrated Suit Technology (JSLIST) was an effort to provide protective garments for military personnel, based on state-of-the-art material technologies. The JSLIST program objectives included addressing heat stress, longer wear, washability and other capabilities. Since this program, the U.S. Dept. of Defense has started to focus on more active features, such as self-cleaning properties.
Textiles with smart properties are created and manufactured in various ways, such as with functional coatings; developing soft composites using fibers; hybrid composites including soft fibrous materials, inorganics and metal filaments; and integrating electronics. The additive components provide active and/or high-performance capabilities, which are not inherent in basic textile substrates. However, in order to be adopted by consumers, smart fabric products must still maintain basic characteristics expected in a textile product, such as drapability, washability, durability, comfort and moisture transfer. This presents a tremendous challenge for the advanced textile industry to address.
Collaborative developments
The recent annual conference of the American Association of Textile Chemists and Colorists (AATCC) that took place in Greenville, S.C. focused on smart textiles in its Materials Track. Among the participants was HeiQ Materials AG, founded as a spinoff from the Swiss Federal Institute of Technology, which partners with textile brands to differentiate and grow through innovation.
One innovative material from HeiQ, evolved out of collaboration with Deakin University near Geelong, Australia, is short polymer fibers (SPF). HeiQi says that its short fibers are the smallest fibers available in the market, with length varying from 1 to 1000 microns and diameter ranging from 0.1 to 5 microns, which can be used to surface finish conventional textiles. Since these short fibers have linear structure, they could integrate thoroughly with the substrates to be functionalized, increasing durability. Deakin University has been pioneering research to develop fiber powders (such as with wool) for a variety of functional applications.
With an ever-increasing need for novel, biobased fibers, Kingsport, Tenn.-based Eastman Chemical Co. is revisiting old concepts to develop new materials for improved functionalities. The fiber, Naia™, is capable of heat setting that gives a smooth appearance and due to its moisture regain can provide a good degree of comfort. This makes its lie between thermoplastic synthetics and a natural fiber like cotton. Blending such biobased fibers with natural and synthetic fibers provides good hand and surface characteristics.
Bioengineering and molecular biology techniques are useful in developing coatings and fibers. The “lotus leaf” effect has been mimicked in textiles to impart super-hydrophobic surface characteristics. This functionality is essential in defense clothing to cause toxic chemicals to slip away quickly from the textile surface.
A presentation by Bolt Threads showed that by using industrial biotechnology approaches, recombinant silk protein could be developed at a commercial scale. Inspired by the a common spider, using molecular biology, Bolt Thread isolated DNA that can be grown in yeast, which, upon fermentation leads to silk powder that can be wet spun to filaments. This development underscores the effectiveness—and the need for—multidisciplinary approaches to develop smart textiles.
There are several other projects using biomimicry to develop new soft materials. A team of researchers from Ithaca, N.Y.-based Cornell University and the Woods Hole, Mass.-based Marine Biological Laboratory have borrowed inspiration from cephalopods, such as octopus, in devising camouflage materials. Scientists took clues from octopus’ morphology to develop synthetic structures which can transform quickly from its two-dimensional structures into three-dimensional shapes, which adapt well with its environment, similar to what an octopus does in real-life situations.
A team of institute-and-industry partners affiliated with Ulsan National Institute of Science and Technology (UNIST) and involving the Korean Institute of Ceramic Engineering and Technology, industrial partner, Yeejoo Co. has used a bacterial pigment Violacein, to impart antimicrobial properties. An indole derivative, Violacein is a violet pigment made by naturally occurring bacteria, such as those belonging to genus such as Chromobacterium. Violacein has been reported to have antimicrobial and antiparasital properties.
When the pigment was coated on the fabric, it was reported to have good efficacy against MRSA and multi-drug resistant Staphylococcus aureus. The coated fabrics inhibited the growth of MRSA and other superbugs by 99.9 percent, according to UNIST. The work could be the first of its kind to effectively utilize bacterial pigment as a coating agent on fabrics to impart antimicrobial properties.
Scientists are also looking into adding biological molecules to add functionality to cotton by adding glucose moieties externally. In fact, the agriculture industry was a pioneer in the use of transgenics in the development of “BT cotton,” by incorporating the Bacillus thuringiensis gene to cotton as a transgene to function as an insecticide against the bollworm. This led to a major improvement in the production of cotton.
Making it wearable
While wearable textiles have become a buzz word in the textiles sector these days to showcase growth and advancement in the field, lack of breathability and comfort has been the barrier for consumer acceptability, as well as the additional cost. At the research level, this field attracts funding and interest among funding agencies and researchers. Minji Kim of Professor Jintu Fan’s laboratory at Cornell University is focusing on this important aspect and discussed how growing piezoelectric ceramics on nanofiber mats, made using piezoelectric polymers such as polyvinylidene fluoride (PVDF), creates a comfortable material with improved piezoelectric effect.
Approaches like electron beam vapor deposition have been borrowed from physics to develop flexible wearable textiles. Professor Suraj Sharma of the Athens-based University of Georgia has developed silver-coated-PVDF piezoelectric nanofiber textiles for energy harvesting purposes. An interesting project is underway at Harvard University that utilizes soft robotics to enhance human performance. Tackling the flexibility aspect of wearable e-textiles was the subject of a talk by Hasan Shahariar of North Carolina State University (NC State), which emphasized the advantages of using conductive dielectric inks.
But is it comfortable?
It is clear from these presentations on wearable textiles that more and more projects are underway to address the subject of comfort, while not losing functional aspects.
Medical textiles offer a fertile field for researchers to explore different functionalities to impart biocidal and microbial resistance characteristics. Although halamine chemistry has been commercially successful, ongoing research in incorporating this chemistry to melt spinnable fibers was explored in detail by Prof. Gang Sun of the University of California, Davis.
Manipulating blending of hydrophilic and other fibers to greige cotton to enable high performance functionalities was discussed by Vincent Edwards of the New Orleans-based U.S. Dept. of Agriculture (USDA) research laboratory. The USDA has been exploring cotton for a variety of advanced applications, such as hemostatic dressings.
Textile materials lend themselves to being combined with several additional components that may include electronics, coatings, metals and inorganic materials. Obviously, these will provide value-added characteristics. However, without comfort, which is the core property of textiles, commercial success and consumer acceptability will be difficult. Time and resources must be dedicated by the advanced textiles industry to tackle this aspect, as we move forward with wearable smart textiles.
Seshadri Ramkumar, Ph.D., is the director of the Nonwovens and Advanced Materials Laboratory, Texas Tech University, and a frequent contributor to Advanced Textiles Source.