Manufacturers new to PPE face challenges in supply chains and specs.
by Janet Preus
The rapid spread of the coronavirus was accompanied by an urgent call for personal protective equipment (PPE), particularly face masks. There were plenty of manufacturers who wanted to join the effort to provide PPE, but they had never made these products before. Cut-and-sew operations, closed as “nonessential” businesses, were willing to reopen and use their facilities, workers and expertise, but they also needed to get up to speed on government specs, sourcing materials and patterning in order to make a product that would work.
With four classes of masks, all designed to perform in specific circumstances, the specifications for each are also different. Connie Huffa, principal, Fabdesigns Inc., explained during an IPC virtual meeting that, “There are a lot of risks associated with medical products, as opposed to fashion, [for example].” She recommended a document available from the U.S. FDA that offers concise information on manufacturing masks.
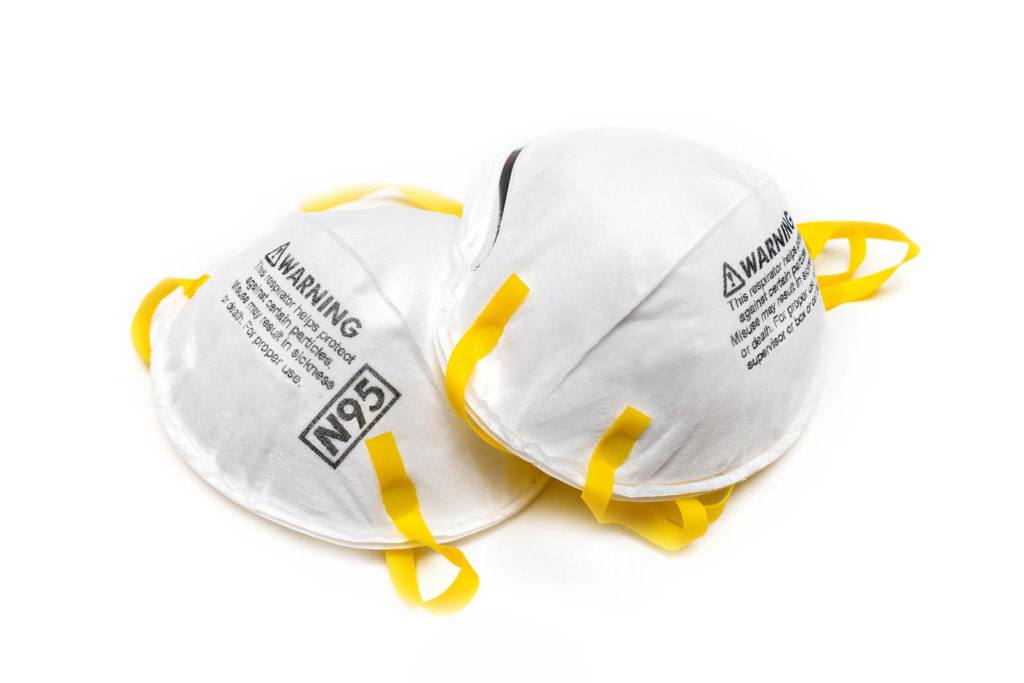
The need for speed
However, in an effort to move quickly, small operations were using what materials they had on hand. Nonwovens, soon in short supply, (even elastic was getting scarce) were being replaced with wovens and knits in order to offer “something rather than nothing” for protection.
Stephanie Rogers, director of product research and development at Apex Mills, told meeting participants, “The woven world is coming in second,” but that will “dry up,” too. Then it will be knits, which don’t fit or perform the same as nonwovens or even wovens. That prompted another meeting participant to suggest that wool fibers could be used to create a dense barrier in a mask.
Rogers described the density like the old “pickup sticks” game. When the fibers are entangled with each other and compacted, it will prevent tiny microbes from going through it. “So, in theory, you can create that dense entanglement [with other fibers, such as wool].”
Linen, which tolerates the high washing temperatures and bleach solution used in hospital laundries, was also suggested as a viable choice for making a reusable product.
Seshadri Ramkumar says that decades ago research by the U.S. Dept. of Agriculture showed that cotton could contain virus spread, because viruses persist for a shorter time on cotton compared to some other materials studied. His lab at Texas Tech University is working with collaborators on improved masks using cotton as the core absorbent material.
The critical N95 masks, however, that are made of spunbond nonwoven layers, also have a meltblown nonwoven layer in the middle and therein lies one of the problems. Meltblown materials take longer to manufacture, so even if other nonwovens could be had, the production of N95 masks was stalled.
Complex decisions
A doctor in Los Angeles, also participating in the IPC meeting, became impatient with the discussion of source materials. “We’re wasting time discussing the wrong thing,” Dr. Markus said. “We’re in desperate need of PPE!”
Furthermore, health professionals treating COVID-19 patients need full PPE, “You need at least an N95, goggles and a face shield, completely dressed and gowned, booties.” But, he notes, administrative workers in hospitals also need protection, and the alternatives to the usual masks and PPE could be given to them, “to keep the N95s for the war zone,” he said.
There’s also the question of fabric treatments. Rogers says medical textiles, including scrubs, generally need barrier protection to prevent fluid transfer. “A DWR [durable water repellent] can address this,” and an antimicrobial can also be added but that can weaken the effectiveness of other treatments.
“If you have to pick between DWR or antimicrobial, pick the DWR,” Huffa says. Doing both could be a waste of money. She also notes that, although the fabric for a mask should be tightly woven, it also needs to be breathable. “Some of the masks have from two to five different layers,” Huffa says, “So it may be that you’re making an overmask to make the N95 last longer; the [over] mask may be removed and sprayed with bleach.”
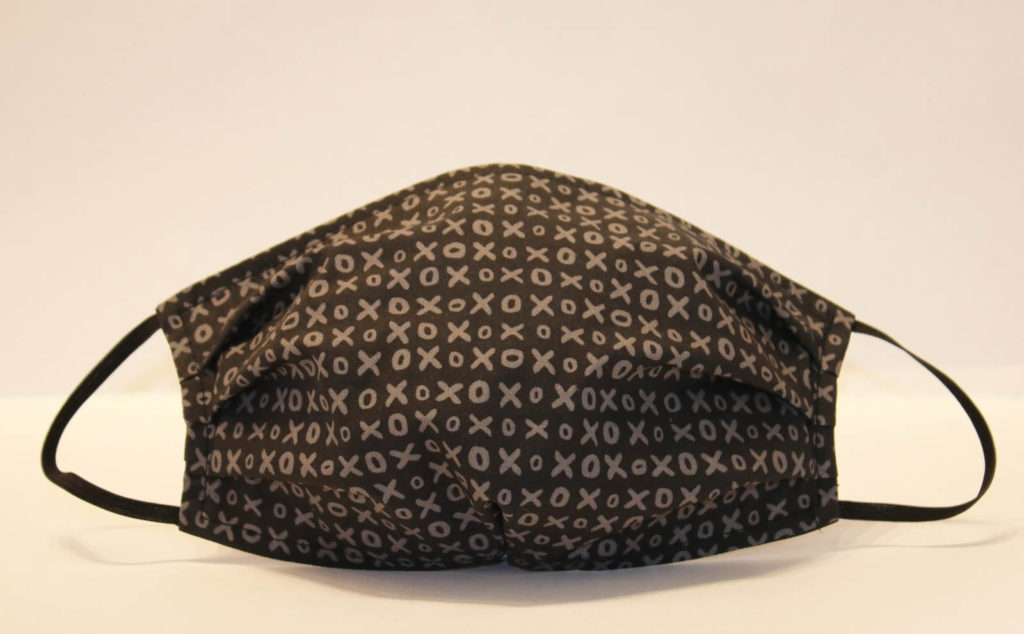
She adds, however, that none of this makes a mask anti-viral. “The virus attaches to other microbes in the air, [that are much bigger than viruses], which can prevent the passage through it,” Rogers says. “It’s like three big football players trying to get through a doorway at the same time.”
In fact, antimicrobials don’t stop viruses, either. “It’s really the reduction of particle movement and the prevention of reaching another person,” she said, which can be accomplished with many kinds of fibers.
Chris Semonelli, chair of IFAI’s Advanced Textile Products, says that, in order to expedite the process and get end products where they need to go, there needs to be “clear specifications and quantities, and reasonable delivery time frames. But there also needs to be some flexibility with technical textile specifications “keeping in mind the finished products function,” he said.
Zack Hurley, CEO and co-founder of indiesource.com, says his company has a reusable, 100 percent USA-made mask available that they’ve offered in a “buy one, donate one” effort to get the masks to health care professionals, service personnel and others who need them. The company, which typically works in the fashion industry, is representative of a number of fashion industry businesses that are venturing into PPE.
Its mask was first designed as a protective cover for N95 masks. As a 2-ply pocketed fabric mask, it functions as a physical barrier and, when paired with a filtered insert, offers enhanced protection. The company stresses that the mask—even with a filter—is not a substitute for an N95 or a surgical mask.
Semonelli feels that industry participants have risen to the challenge. “I have never seen a period when people in our industry want to help so much,” he says.
Paige Mullis, director of concept development with Glen Raven, says, “Things we’re putting in place today as reactive, might become the way we operate day-to-day.”
Janet Preus is senior editor of Advanced Textiles Source. She can be reached at jlpreus@ifai.com.