As information on coronavirus becomes available, face covers and PPE specifications and standards should be developed in response.
by Seshadri Ramkumar
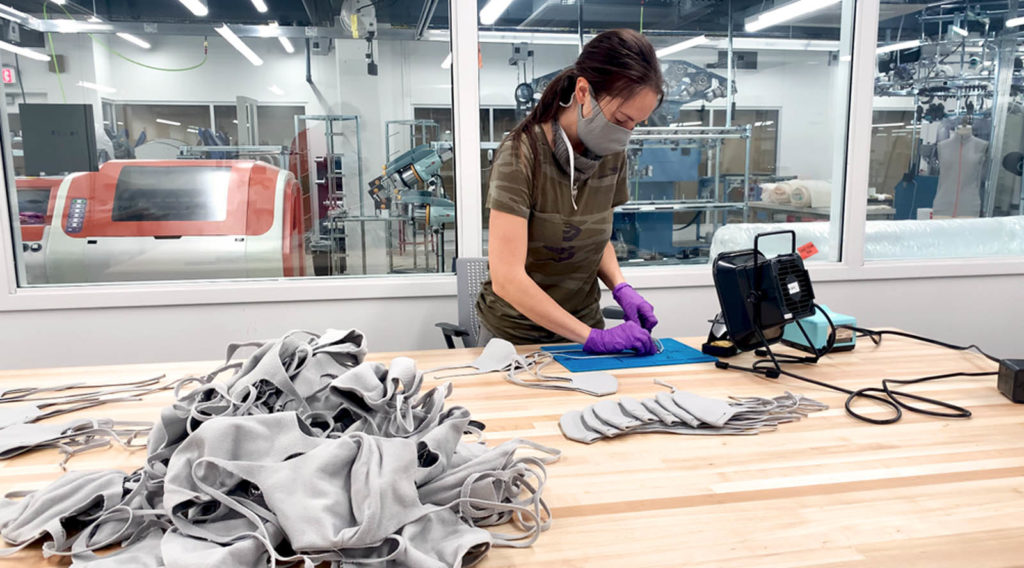
On June 18, Governor Gavin Newsom of California issued a statewide order mandating face cover use in public places and areas where social distancing is not feasible. Although a brief description of “face covers” has been provided in the mandate, performance specifics and standard requirements have not been listed. In fact, no specifications or standards for these face covers have emerged since COVID-19. This is a typical scenario of the “new normal,” which emphasizes the need to rapidly modify and/or develop new standards and establish specifications for new products.
The need for new products
The COVID-19 situation has put a spotlight on multiple types of personnel protection equipment (PPE), but with the current information, as well as emerging studies, the mode of transmission of the virus, remedies and countermeasures are still not well understood. This means that the circumstances regarding new products and standards are dynamic.
PPE is critically needed because of the nature of the virus and its mode of transmission. A better understanding of this will enable the development of products that address specific aspects. Among the modes of transmission, movement of the virus as moisture droplets seem to be the most widely accepted. Another theory is that smaller virus particles of size 0.3 microns or less can be airborne, which enables them to travel for longer distances and persist in the atmosphere for a longer duration.
The intensity of the transmission and the spread of the infection depends on the size of virus particles, the viral load and the mode of transmission. Particularly with the current COVID-19 situation, still more research is needed on this. These aspects, however, play an important part in understanding how to develop proper face masks, surgical gowns, and other non-medical countermeasures, and some modification of the existing standards may be required.
The need for standards
Requirements for defining specifications and standards depend on science, but also end-user expectations. Although filtration efficiency is the most important functional attribute of a face mask, based on feedback from end-users such as physicians, other aspects, such as breathability and comfort, fluid resistance and flame spread, have to be taken into account.
“Not only functional aspects are important. Face masks’ use and acceptability depend on their comfort and fit. Therefore, while developing standards, focus should be holistic and involve all components,” says Dr. Manickavasagam Sundaram, department of medicine, Lakeridge Health, Oshawa, Canada.
Although there are established and globally accepted standards for Filtering Face Piece Respirators (commonly referred to as N95 masks), standards have to be developed for face covers and filter-enhanced covers known as “FISORS.” One size fits all will not be much help as these products are meant to cater to different scenarios, such as enhancing social distancing. Although there is ongoing debate about the effectiveness of face covers to counter the viral spread, these are being recognized as an important enhancement of social distancing, as is evident from Gov. Newsom’s order.
New standards evolution
Standards are normally evolved to deliver needed products of high quality that meet the requirements for a particular task. These are developed based on stringent user and safety expectations, as well as consensus among end-users, product developers and standardization agencies.
In the case of face masks, depending on the nature of application—such as medical or defense—specific requirements and standards may vary. Different product manufacturers evaluate the product against requirements in multiple laboratories to arrive at consistency so that universal standards and text methods can be developed. This process involves collaboration and cooperation among stakeholders.
As the need and use of different types of face masks emerge, specifics concerning the materials, structure, performance and comfort attributes have to be determined. This is more complicated for face covers, as the developers of these products and end-users are on such a broad spectrum, which adds to the complexity—a new normalcy indeed!
“Standards are derived internationally after extensive scientific discussions and research. It is important that they not only assure the user of the suitability of a product for the intended end use, but also facilitate creating an ecosystem that ensures its continuous availability,” says Dr. Prakash Vasudevan, director of the Coimbatore-based South India Textile Research Association.
Science-based standards development
Standards for product development and testing evolve appropriately when they are based on peer-reviewed science, need and cooperation. A case in point are the recent changes made by the U.S. Occupational Safety and Health Administration (OSHA) to the Respirator Protection Standard.
In accordance with more than one scientific study, OSHA reduced the number of fit exercises that led to shorter test duration. Based on revisions, instrument makers help the users to adapt the existing machines to conform to the new guidelines. For example, modified ambient aerosol fit test methods are updated in the TSI PortaCount tester to comply with the new standard. Cooperation among instrument makers and end-users has reduced the compliance burden without comprising the quality aspects.
The necessity of standardization
Generally, a new standard or modification to the existing ones evolve based on situation, need and new applications. We are witnessing this situation with the need for different types of face masks such as face covers, FISORS and similar. The need must be justified, arising from new findings, societal needs and urgency. Again, using face covers as an example, a recent study by a team of researchers led by Texas A&M has shown, based on data and projections, which face covers have prevented over 66,000 infections in a month’s time in New York City.
Professor Renyi Zhang of Texas A&M, co-author of the study, said that the mandated use of face covers has helped with containing COVID-19 in China. While it is an established understanding that N95 masks offer the best possible protection against aerosol particles, the above study emphasizes the importance of alternative face protection, as well, to counter the pandemic.
Professor Mario Molina, Nobel Laureate and co-author of the study, has said that face masks help to prevent the transmission of droplets and safeguard an uninfected person from inhaling the particles. Standards for face covers and FISORS need to be developed quickly, based on scientific studies, as well as on a consensus among stakeholders. This is need-based standardization, where speed of standardization and the determination of specifics play important roles.
The importance of quality
Although COVID-19 has created a new normalcy, it does not mean quality should be compromised. Early on in the COVID-19 scenario, when there was a lack of availability of N95 masks, the end-user community seriously looked at different decontamination methods. A good understanding about reusing masks and decontamination protocols needed “buy-in” by medical practitioners, government agencies and the public.
“First and foremost, basic requirements of PPE products are to maintain high quality standards to avoid any transmission of virus during usage. Unfortunately, it is observed in many cases that some of the new products are sub-standard,” says Dr. Anup Rakshit, executive director of Mumbai-based Indian Technical Textile Association.
“Probably the manufacturers are not able to produce these products with consistent quality due to lack of understanding of product standards and appropriate quality management systems (QMS) are not in place in their manufacturing factories,” he adds. “It is therefore necessary that PPE coverall and mask manufacturers implement QMS systems as per ISO-13485/ISO-9001 and follow international guidelines to become a trusted supplier of medical textiles.”
A way forward
Developing standards is critical to cater to the requirements of a particular application, safety needs, and acceptability by the end-user community. As the need emerges, modifications to existing standards have to be considered. In the present globalized economy, harmonized standards will be the way to go. Attention must be given to the quality of products, even in times when resources are in short supply.
Seshadri Ramkumar, Ph.D., is a professor in the Nonwovens and Advanced Materials Laboratory, Texas Tech University, and a frequent contributor to Advanced Textiles Source.